Vacuum die casting technology has a wide range of applications in several metal industry production fields.
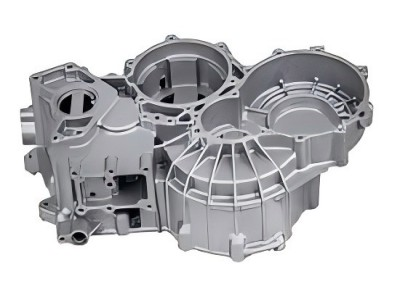
Especially in the need to improve product quality and reduce the defect rate of occasions.
Widespread application of vacuum die-casting technology
We follow the actual case to list some of the main applications of vacuum die casting:
- Automotive parts manufacturing
- Magnesium alloy seat frames:
- Photovoltaic material production
- Aluminium parts production
- Other applications
Automotive parts manufacturing:
Vacuum die casting technology is commonly using produce automotive parts, such as the rear shell of the car compressor.
By using a high vacuum system, the internal porosity can be significantly reduced, and the denseness and strength of the product can be improved.
For example, the use of high vacuum die casting technology production of aluminium rear shell, its internal porosity than non-vacuum system reduced by 57.8%, and the defect rate is only 0.17% .
Magnesium alloy seat frames:
Vacuum die casting technology is present in the manufacture of magnesium alloy seat frames.
This technology reduces porosity, improves surface appearance, and allows for the manufacture of larger parts because high pressure die casting is not required.
Components produced using vacuum systems have higher strength and elongation than normal high-pressure die-cast parts.
Photovoltaic material production:
Vacuum die casting technology produces silicon wafers suitable for photovoltaic cells.
This technology improves the performance and productivity of photovoltaic materials by optimising the silicon nitride material composition and surface treatment.
Aluminium parts production:
Vacuum die casting technology is widely used in the production of various types of aluminium parts.
By applying vacuum inside the mould, the air in the mould can be effectively excluded, thus improving the mechanical properties and density of the castings.
Using high vacuum die casting technology to produce dumbbell specimens, its porosity reduced by 5.47%, the maximum stress increased by 4.83% .
Other applications:
Vacuum die casting technology is also used in other areas, such as the production of parts with complex shapes and high precision requirements.
This technology improves the overall quality and reliability of products by reducing porosity and cold joint defects .
Vacuum die casting technology provides an efficient, high-quality solution for many industrial sectors by reducing porosity, increasing density and improving surface quality.
These advantages make vacuum die casting an integral part of modern manufacturing.
Vacuum die casting applications on automotive components
Vacuum die casting technology has a wide range of applications in the manufacture of automotive parts very.
Especially in the production of engine cylinder block, cylinder head and transmission housing and other components.
The following is a detailed description of these applications:
- Engine cylinder block and cylinder head
- Transmission shell:
- Other related applications
Engine cylinder block and cylinder head:
Vacuum die casting technology offers significant advantages in the manufacture of engine cylinder blocks and cylinder heads.
These components require high strength and heat resistance to ensure engine reliability and performance.
The use of vacuum die casting reduces porosity defects and improves surface finish and dimensional accuracy, thereby enhancing the overall quality of the component.
During the manufacturing process, vacuum die casting technology can effectively control the entry of gases, making the internal structure of the casting more uniform.
Reduced defects due to gas trapping.
Transmission shell:
Transmission shell is an important part of the automobile transmission system, need to have good mechanical strength and durability.
The application of vacuum die casting technology in this field helps to produce lighter and stronger transmission cases.
Through vacuum die casting, finer surface finishes and higher dimensional accuracy can be achieved, which is crucial to improving the durability and reliability of transmission cases.
Other related applications:
Vacuum die casting technology is not only to the above components, but is also widely used in the manufacture of other automotive parts, such as intake manifolds and suspension components.
In these applications, vacuum die casting technology improves the overall quality and performance of components by reducing porosity and improving surface finish.
Vacuum die casting technology has important application value in the manufacture of automotive parts.
Especially in the production of key components that require high strength, high precision and durability such as engine cylinder block, cylinder head and transmission housing.
This technology significantly improves the quality and performance of components by reducing porosity defects and improving surface finish.
Vacuum die casting for photovoltaic material applications
The application of vacuum die casting technology in magnesium alloy seats is to greatly improve the quality of the product.
Mainly embodied in the following aspects:
- Improve the mechanical properties and appearance quality
- Reduce weight and meet safety requirements
- Optimise the production process
- Improve casting quality and production efficiency
- Integration with other processes
Improve mechanical properties and appearance quality:
Vacuum die casting technology can significantly reduce the porosity of magnesium alloy products, thus improving the surface appearance quality.
Compared with the traditional high pressure die casting, vacuum die casting can achieve more complete filling and better surface effect.
In addition, vacuum die-cast magnesium alloy parts have improved mechanical properties.
For example, strength and elongation have increased by 14.2% and 43.7% respectively.
Reduce weight and meet safety requirements:
Through vacuum die casting technology, the design of magnesium alloy seat frames can achieve weight reduction.
The design of magnesium alloy seat frame reduces the weight by 10% than the traditional steel seat frame.
And the safety test procedure of the seat frame was simulated by finite element method to ensure that it meets the safety regulations.
Optimising the production process:
Vacuum die casting technology does not require the high pressures of conventional high-pressure die casting and can therefore be used for the production of large components.
It also reduces problems with cold joints and overflow chambers.
This technology also allows for higher temperatures and longer heat treatments.
This further improves the overall mechanical properties of magnesium alloys.
Improve casting quality and production efficiency:
Vacuum die casting technology by pumping vacuum in the injection chamber and mould cavity.
It improves the casting quality and solves the problem of flammability of magnesium alloy.
And overcome the porosity defects, improve the production efficiency of the finished product.
Combination with other process:
Vacuum die casting technology is often used in combination with other processes such as semi-solid casting and squeeze casting.
To further enhance the performance and application of magnesium alloy parts.
Vacuum die casting technology in the application of magnesium alloy seats improve the mechanical properties and appearance quality of the product.
Also through the reduction of weight and optimisation of the production process to meet the needs of the modern automotive industry for lightweight and safety.
Proven vacuum die casting technology application of haichen die casting machine
Haichen die casting machine excels in the application of vacuum die casting technology.
Vacuum die casting technology is an advanced die casting process, through the die casting operation in a vacuum environment.
Can effectively avoid the problem of oxidation and gas absorption, thus improving the quality of castings.
The main advantages of vacuum die casting technology include reduced porosity of castings, improved surface finish, enhanced dimensional accuracy and uniform microstructure.
Haichen applies vacuum die casting technology to prevent the formation of porosity by using a powerful vacuum system to reduce the air pressure in the mould cavity, ensuring minimal gas residue.
This technology is not only suitable for aluminium, magnesium alloy die casting, but also can be used for zinc alloy and other low melting point alloy die casting.
In practical application, vacuum die casting technology can significantly reduce the porosity of aluminium alloy castings, improve internal quality.
Improve the hardness and mechanical properties of castings.
In addition, vacuum die casting technology is also widely used in the production of automotive parts.
Such as gearbox shell and clutch shell and other complex parts manufacturing.
These parts usually need high precision and high strength performance, vacuum die casting technology can meet these requirements.
In the vacuum die casting process of the clutch housing, multi-directional high-speed real-time control of the evacuation system using to optimise the casting process.
To eliminate porosity and shrinkage defects in aluminium alloy castings.
Haichen die casting machines have demonstrated excellent performance and reliability in the application of vacuum die casting technology.
By combining advanced hydraulic and electrical systems with sophisticated design.
Haichen die casting machine can meet the production needs of different materials and complex parts.
This improves production efficiency and product quality.