Die casting process benefits involves that can produce high – precision parts, strong and durable parts, high production efficiency and material versatility. Die casting process benefits and limitations affect the productivity of die casting.
And die casting is a manufacturing process used to produce precision metal parts by forcing molten metal under high pressure into a mold cavity.
The die casting process occupies an important place in modern manufacturing due to its efficiency, precision and significant cost-effectiveness. However, its high tooling costs, material limitations, risk of internal defects and limitations on the production of large parts also make it limited in certain application scenarios.
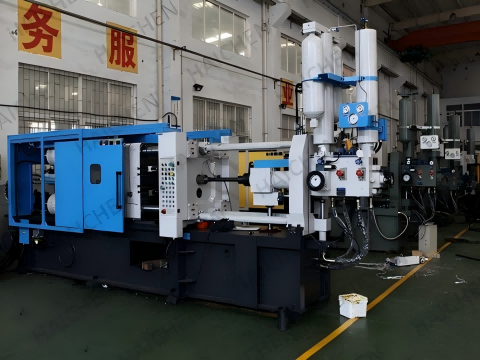
Die casting process benefits
- High Production Efficiency
- Precision and Consistency
- Versatility in Materials
- Cost-Effective for Large Volumes
- Complex Geometries
- Strength and Durability
- Surface Finish
- Recyclability
High Production Efficiency:
Die casting enables the rapid production of complex shapes with tight tolerances and smooth surfaces, making it suitable for large-scale manufacturing.
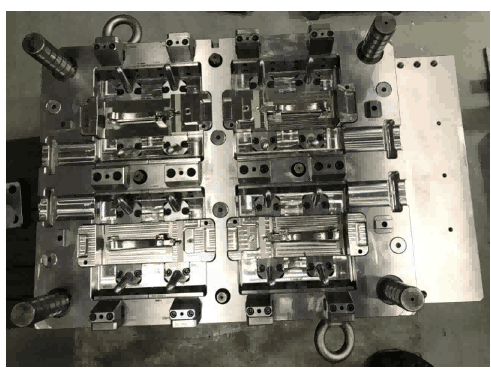
Precision and Consistency:
The process produces parts with excellent dimensional accuracy and uniformity, reducing the need for secondary machining.
Versatility in Materials of die casting process benefits and limitations:
Die casting is compatible with a wide range of non-ferrous metals such as aluminum, magnesium, zinc, and their alloys.
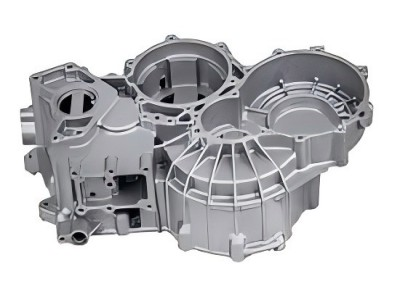
Cost-Effective for Large Volumes:
High initial tooling costs are offset by low per-unit costs in mass production, making it economical for large production runs.
Complex Geometries of die casting process benefits and limitations:
Enables the creation of intricate designs, thin walls, and detailed features that are difficult to achieve with other manufacturing processes.
Strength and Durability:
Produces parts with good mechanical properties, including high tensile strength and durability.
Surface Finish of of die casting process benefits and limitations:
Provides a smooth surface finish, which can be further improved with minimal finishing processes like polishing or coating.
Recyclability of die casting process benefits and limitations:
The process supports the recycling of materials, reducing waste and making it an environmentally friendly option.
Die casting process limitations
- High Initial Cost
- Material Restrictions
- Porosity Issues
- Size Limitations
- Limited Wall Thickness
- Tooling Wear
- Not Ideal for Prototyping
- Thermal Fatigue
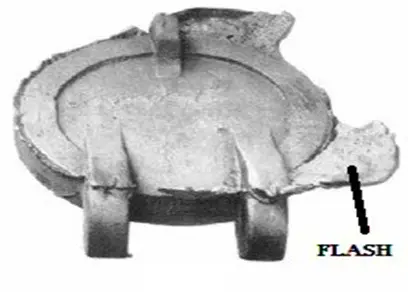
High Initial Cost of die casting process benefits and limitations:
The process requires significant upfront investment in tooling and machinery, making it less suitable for small production runs.
Material Restrictions:
Only works with non-ferrous metals, limiting its application for certain industries and materials.
Porosity Issues:
Trapped air during casting can result in porosity, reducing the mechanical strength and surface finish of the parts.
Size Limitations:
Best suited for relatively small to medium-sized parts due to the size constraints of die-casting machines.
Limited Wall Thickness:
Producing very thick sections can be challenging due to cooling and solidification constraints.
Tooling Wear:
The dies experience wear and tear due to the high pressures and temperatures, leading to maintenance and replacement costs.
Not Ideal for Prototyping:
The high cost and time required to produce dies make it unsuitable for rapid prototyping or short-term production.
Thermal Fatigue:
Repeated heating and cooling cycles can cause thermal fatigue in the die, potentially affecting dimensional accuracy and lifespan.
What is Die Casting?
Die casting is a manufacturing process used to produce high-quality, complex metal parts with tight tolerances and excellent surface finishes. It involves forcing molten metal into a reusable mold (called a die) under high pressure.
How Can You Minimize the Die Casting Defects?
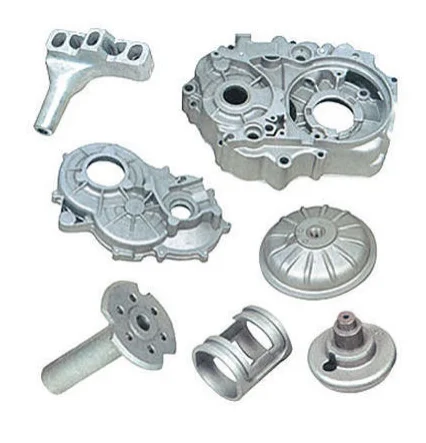
Minimizing die casting defects requires a comprehensive approach that addresses various aspects of the process, including mold design, process parameters, and material handling. Here are some effective strategies:
Optimize Process Parameters
- Injection Pressure and Speed: Adjusting injection pressure and plunger velocities can significantly reduce defects such as porosity and cold shut. For example, optimizing injection pressure and speed can improve part density and reduce porosity by up to 61%.
- Cooling Time and Rate: Controlled cooling rates can reduce internal porosity and shrinkage defects. Implementing gradual cooling helps dissipate trapped gases more effectively.
- Mold Temperature: Maintaining optimal mold temperature can prevent issues like burn marks and improve overall casting quality.
Improve Mold Design
- Tight Tolerances and Precision: Incorporating tighter tolerances in mold design and using advanced CAD/CAM technologies can reduce misalignment and flash formation.
- Venting and Overflow Systems: Adequate venting allows air to escape from the mold cavity, reducing the risk of gas-related defects. Proper vent placement can cut flash formation by up to 30%.
Haichen die casting machine
Haichen, a manufacturer which is specialized in cold chamber and hot chamber die casting machines, auxiliary eqiupments and spear parts. and widely recognized for efficiency and precision in the production of high-quality cast parts. We are commonly used in industries such as automotive, aerospace, electronics, and consumer goods for manufacturing components from materials like aluminum, zinc, and magnesium.
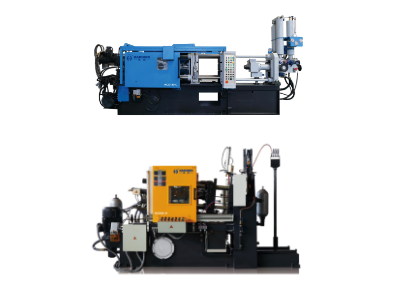
If there is any information about the die casting want to know, welcome to consult us.
The die casting process has significant advantages in terms of improving productivity and ensuring dimensional accuracy and surface quality.
But its high initial cost, material selection limitations and dependence on mass production are its main limitations.
Therefore, when selecting die casting as a manufacturing method, above factors need to be considered comprehensively to ensure its applicability and economy.