Cold Chamber Die Casting is a precision casting process for high melting point metals such as aluminium, copper and brass.
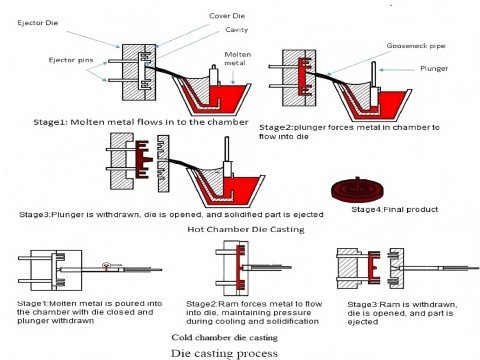
Its main features and steps are as follows:
1. Cold chamber die casting mould preparation:
First of all, it is necessary to design and manufacture the mould (also known as tooling or mould), which usually consists of two steel blocks, including the die-casting mould and other special parts such as the gating system.
2. Die casting metal melting and preparation:
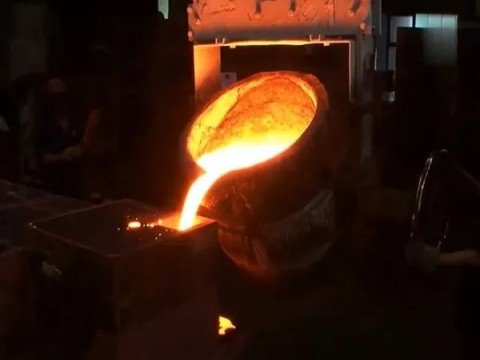
The molten metal is heated to its melting point in a separate die casting furnace and then poured through a gate into a cold chamber (i.e., the injection chamber).
This process avoids direct contact between the metal and the injection system, thus reducing corrosion problems.
3. Metal pressure injection:
A high pressure hydraulic piston pushes the molten metal from the cold chamber into the mould cavity.
Due to the high pressure (typically between 20 and 350 MPa), the metal is able to completely fill the mould and form the desired geometry.
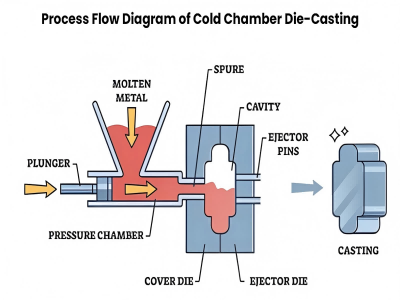
4. Curing and cooling:
After completing the metal injection, the cold chamber die casting machine locks the mould to keep it tight.
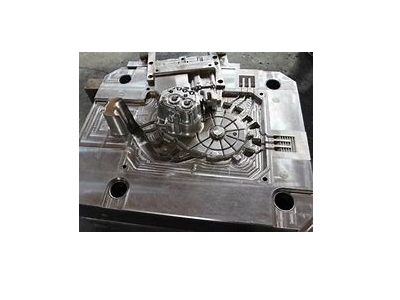
The metal is allowed to cure and cool inside the mould.
This stage ensures the dimensional accuracy and surface quality of the product.
5. Cold chamber die casting product removal:
After the die casting product cools down, the cold chamber die casting machine opens the mould and uses a robot to automate or manually enter the mould to remove the finished product.
The advantages of the cold chamber die casting process lie in its ability to produce parts with high precision and complex geometries, while avoiding the corrosion and damage to equipment systems caused by high temperatures.
In addition, because the melting process is separate from the casting process, the temperature and quality of the metal can be better controlled, resulting in fewer impurities and defects.
The choice of cold chamber die casting requires careful analysis based on specific application requirements and material properties.
Cold Chamber Die Casting Mould Preparation Process
The preparation process of cold chamber die casting mould is an important part of the die casting process.
Directly affect the quality of the final product and production efficiency.
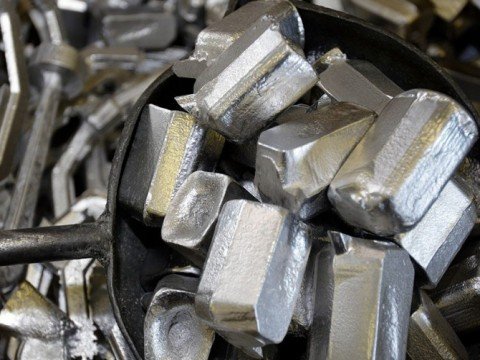
The following are the detailed steps of the cold chamber die casting mould preparation process:
1. Mould installation and inspection:
Firstly, load the mould onto the die-casting machine and replace the plunger and plunger sleeve according to the weight of the casting to ensure that the mould can withstand the corresponding pressure.
Check that all parts of the mould are in good condition, including the hydraulic system, injection system and the cleanliness of the mould itself.
Ensure that the surface of the mould is smooth and free from impurities and apply a suitable lubricant or release agent to prevent the molten metal from adhering to the surface of the mould.
2. Mould preheating:
After the mould has been installed, preheat the mould to a set temperature. This step helps to improve the life of the mould and the quality of the castings.
3. Adjustment of mould parameters:
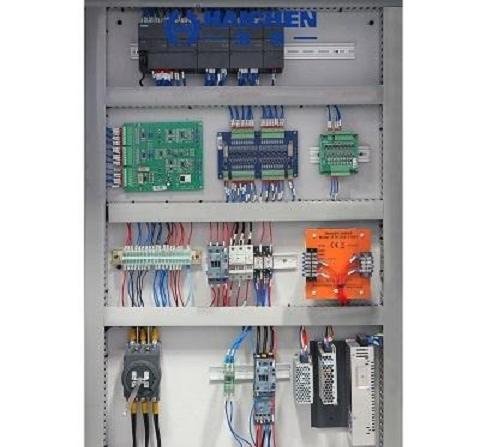
According to the requirements of the casting, adjust the parameters of the mould, such as the pitch of the fixed template and the ejection distance, to ensure that the mould can be formed correctly.
Setting the pouring position, usually bottom pouring is adopted to avoid defects caused by improper pouring position.
4. Equipment commissioning:
Before starting the equipment, check whether all safety protection devices work properly and confirm the normal operation of temperature control system and cooling system.
Set the operating parameters such as injection speed, pressure, holding time and cooling time to ensure that the metal liquid can fill the mould evenly and cure quickly.
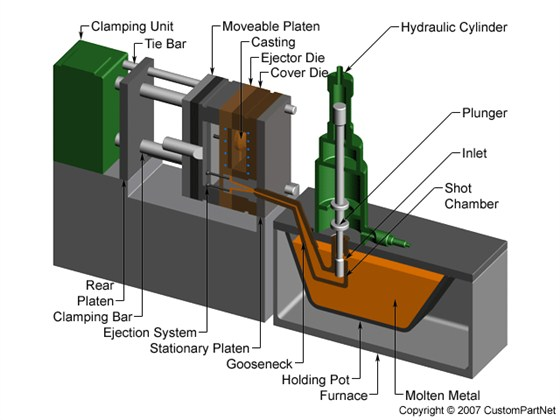
5. Prepare the metal liquid:
Heat the metal material to a liquid state and add alloying elements as needed to improve casting properties.
Ensure that the liquid metal is at the right temperature, usually between 700°C and 800°C, so that it capable to injecting into the mould under high pressure.
6. Mould closing and clamping:
After completing the above preparations, close the mould and apply clamping force by means of a hydraulic system to ensure that the mould does not open during the high pressure injection process.
7. Spraying mould release agent:
After the mould has been closed, a release agent is sprayed to further prevent the liquid metal from adhering to the surface of the mould.
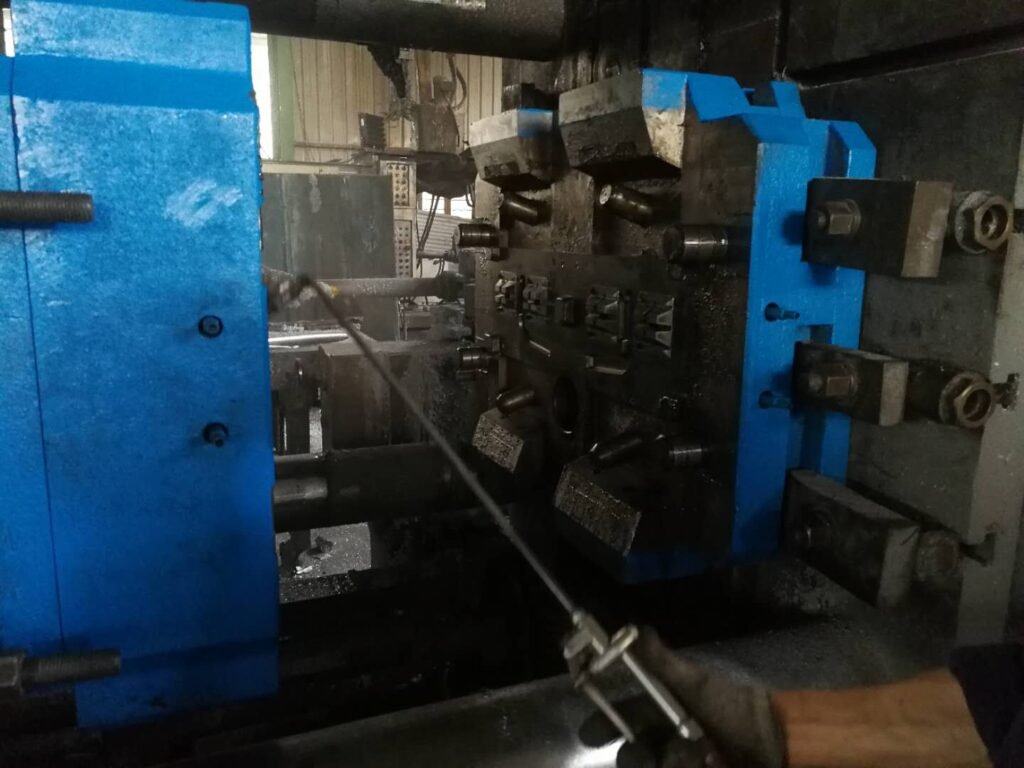
8. Prepare for pouring:
Pour the molten metal into the preheated sprue system and wait for the liquid metal to cool down to a temperature suitable for injection.
Through the above steps, it can be ensured that the preparation of cold chamber die casting moulds is adequate and meets the production requirements, thus improving the quality of castings and production efficiency.
Cold chamber die casting metal melting process
The cold chamber die casting metal melting process is one of the key steps in the die casting process.
Its main purpose is to heat the metal material to a liquid state for injection into the mould.
The following is a detailed description of the die casting metal melting process:
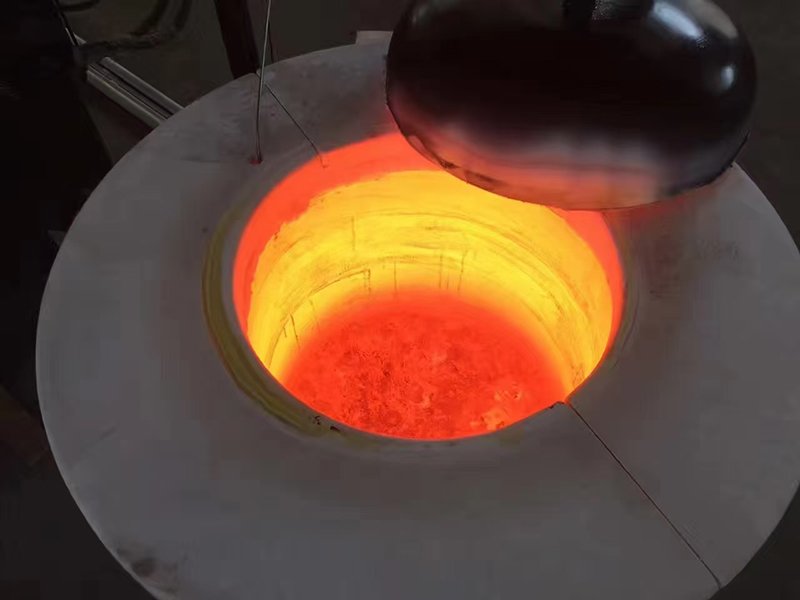
1. Melting temperature and method:
1.1 Metals commonly used in the die casting process include aluminium alloys, zinc alloys and magnesium alloys.
The melting point of these metals is low, usually between 600°C and 750°C.
For example, the melting temperature of aluminium alloys is generally 600-700°C, while that of zinc alloys is about 400-430°C.
1.2 The melting process is usually carried out in high-temperature furnaces, using either electric or natural gas heating.
For example, aluminium alloys may be melted by heating in a resistance furnace, whereas zinc alloys are melted by electric heating.
2. Control during melting:
2.1 During the melting process
The temperature and time need to be strictly controlled to ensure that the chemical composition of the metal liquid meets the requirements and a good crystalline organisation is obtained.
For example, aluminium alloys need to be kept at a temperature of about 670°C during melting, while zinc alloys are melted at a temperature of about 400°C to 430°C.
2.2 Smoke and exhaust gases
They may be generated during the melting process, so it needs to be equipped with a gas collection system for treatment.
3. Treatment after melting:
3.1 After melting,
Will need to treadt the metal liquid with slag removal and degassing to remove impurities and oxides.
For example, aluminium alloys require the addition of a slag remover after melting to reduce impurities.
3.2 The molten metal liquid
Usually conveyed to a holding furnace to maintain its temperature before it is injected into the mould.
4. Precautions during melting:
4.1 During the melting process,
The interaction between the liquid metal and the crucible may lead to gas entrapment and gas absorption.
This may affect the quality of the final product.
4.2 The melting furnace
Will needs to regularly clean slag and impurities to ensure the smooth running of the melting process.
The cold chamber die casting metal melting process is a complex and critical step. that requires precise control of temperature, time and chemical composition to ensure that a high quality liquid metal is obtained and to reduce defects in production.
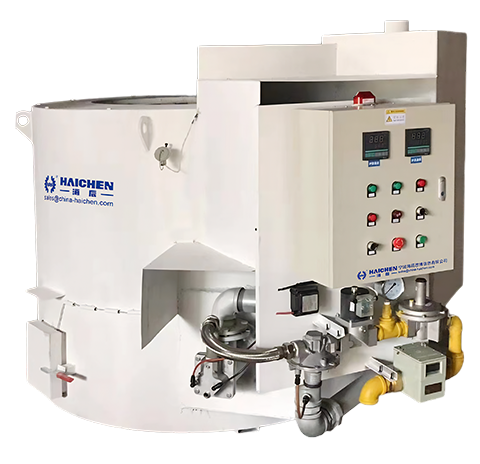
Cold Chamber Die Casting Product Robot Removal Process
The removal of cold chamber die casting product robot is an important step in the automated production of die casting.
The process involves a number of steps, mainly including mould inspection, casting removal and casting placement of the three main links.
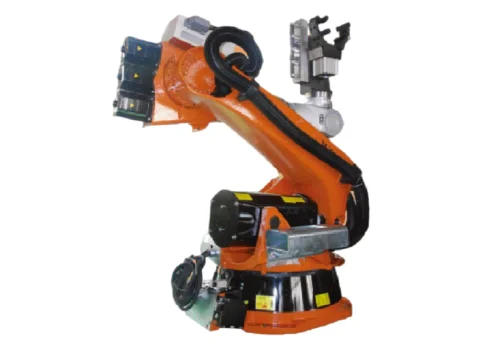
The following is the detailed removal process:
1. Mould detection:
First, the robot will detect the state of the mould to ensure that the mould has cooled down and is ready for the take-out operation.
This step is important to ensure the quality of the castings.
Because if the mould is not completely cooled, it may lead to deformation or damage of the casting.
2. Remove the casting:
When the mould status is detected, the manipulator starts to perform the pick-up action.
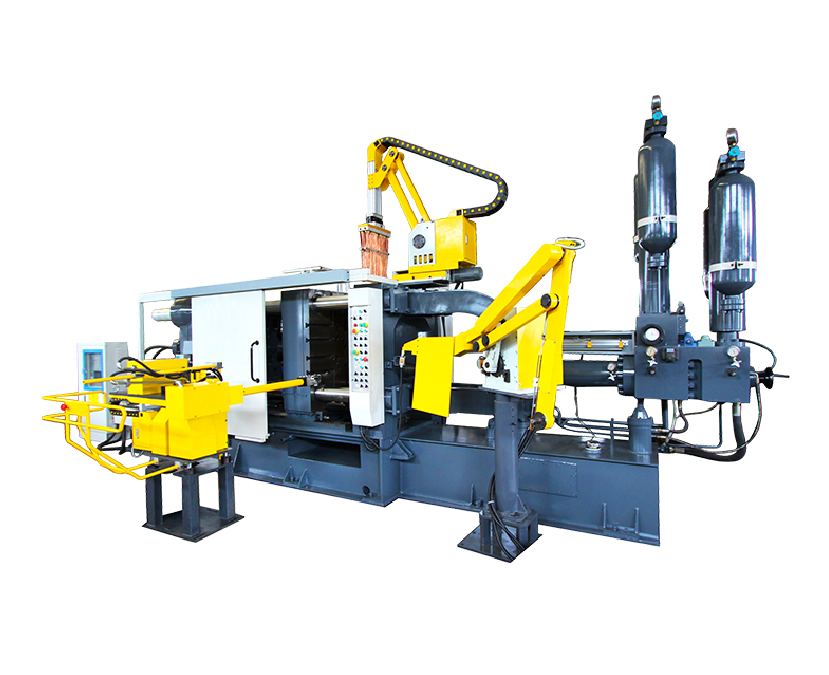
Specifically, the robot removes the casting from the mould by rotating, moving in and out, lifting and lowering.
This process requires precise control of the position and speed of the robot to avoid damage to the casting.
When removing the casting, the robot typically utilises high precision sensors to ensure the integrity and positional accuracy of the casting.
3. Place the casting:
After removing the casting, the robot will place the casting in the specified location.
This step also requires precise control to ensure that the casting is stable on the conveyor belt or in the designated processing equipment for subsequent processing.
Throughout the process, the operation of the manipulator is highly automatical, reducing manual intervention and increasing productivity and safety.
In addition, some advanced cold chamber die casting machine is also equiping with spray function, can be in the process of picking up the casting for preliminary cooling treatment, further improve the quality of castings.
The pick-up process of Haichen’s cold chamber die casting product manipulators is a highly automatical and precise operation process.
Through the use of multi-joint robotics and intelligent control systems, Haichen achieves efficient and safe casting removal and placement.
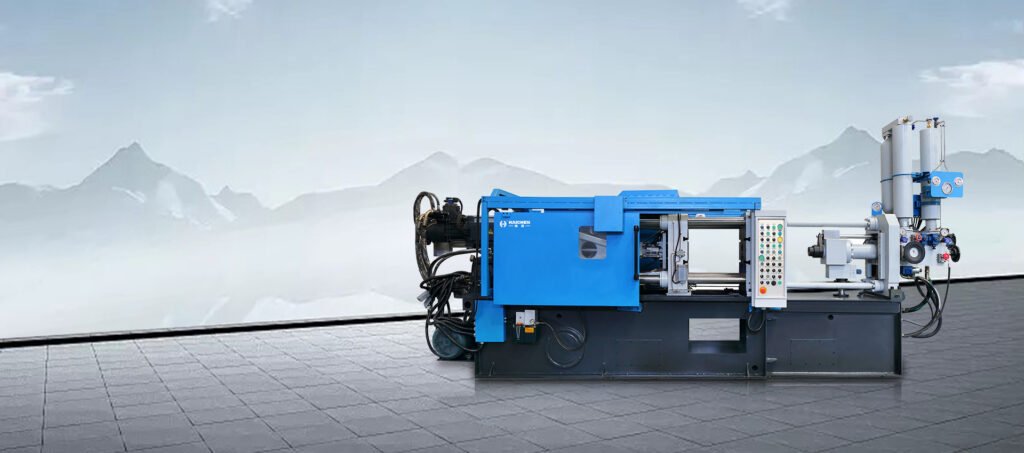