Cast aluminum alloys occupies an important position in the industry because of its excellent casting properties, mechanical properties and adaptability.
According to the alloying elements and performance requirements, cast aluminum alloys can be divided into five categories.
Al-Si series, Al-Cu series, Al-Mg series, Al-Zn series and special cast aluminum alloys such as Al-Fe-RE alloys.
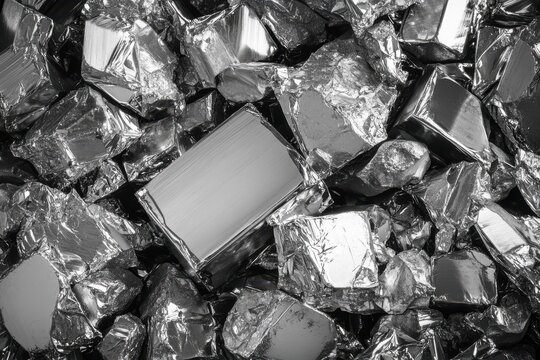
Al-Si cast aluminum alloy
Chemical composition
Silicon (Si) content: 4%~13% (generally near eutectic composition).
Other elements: Copper (Cu) and magnesium (Mg) are often added to enhance mechanical properties.
Such as the EU brand AlSi7Mg containing Si 6.5~7.5% and Mg 0.25~0.45%.
Typical grades: ADC12, A380, A356, ZL102, etc.
Mechanical properties
Tensile strength (UTS): 145~384 MPa (higher value can be reached after heat treatment.
Such as 384 MPa for Al-7.01Si-0.62Mg alloy UTS in T6 state).
Elongation (A): 1.6%~11.3%. Hardness: 194.8~542 MPa.
Applications
Automotive industry: large thin-walled complex parts such as shock absorbing towers, subframes, hydraulic pump housings, etc.
Aerospace: engine blocks, aircraft structural parts.
General industry: instrument housings, pistons, motor housings.
Advantages and disadvantages
Advantages: good fluidity, low hot cracking tendency, strong corrosion resistance, suitable for precision casting.
Disadvantages: The unmodified Al-Si alloy has low tensile strength and needs to be strengthened by heat treatment or adding elements.
Al-Cu cast aluminum alloy
Chemical composition
Copper (Cu) content: 4.5%~5.3% (the best strengthening effect).
Other elements: manganese (Mn),titanium (Ti) are added to improve high temperature strength and casting performance.
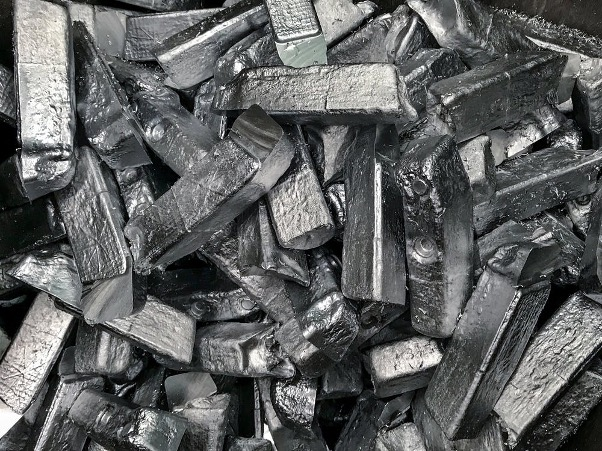
Mechanical properties
Tensile strength (UTS): 240~415 MPa (for example, Al-0.42Si-0.58Mg alloy is 240 MPa after T6 treatment).
High temperature performance: It still maintains high strength at 200~300°C.
Fields of application
High-temperature environment: engine parts, aviation high-temperature parts.
High-load structural parts: sand castings such as transmission boxes, suspension system parts.
Advantages and disadvantages
Advantages: high strength, excellent heat treatment strengthening effect.
Disadvantages: poor corrosion resistance, poor casting performance (easy to hot cracking).
Al-Mg cast aluminum alloy
Chemical composition
Magnesium (Mg) content: about 12% (minimum density and highest strength).
Other elements: Iron (Fe) content (<0.2%) is strictly controlled to avoid brittle phases.
Mechanical properties
Tensile strength (UTS): 214~415 MPa (such as ZL301 alloy).
Elongation (A): 5%~14.8%.
Corrosion resistance: Excellent performance in the atmosphere and seawater.
Fields of application
Shipbuilding industry: propellers, marine pump bodies.
Military industry: radar base, aircraft landing gear.
Corrosion-resistant parts: chemical equipment, sea vessel accessories.
Advantages and disadvantages
Advantages: excellent corrosion resistance, good comprehensive mechanical properties at room temperature.
Disadvantages: poor casting performance (easy oxidation in melting), mechanical properties are greatly affected by wall thickness.
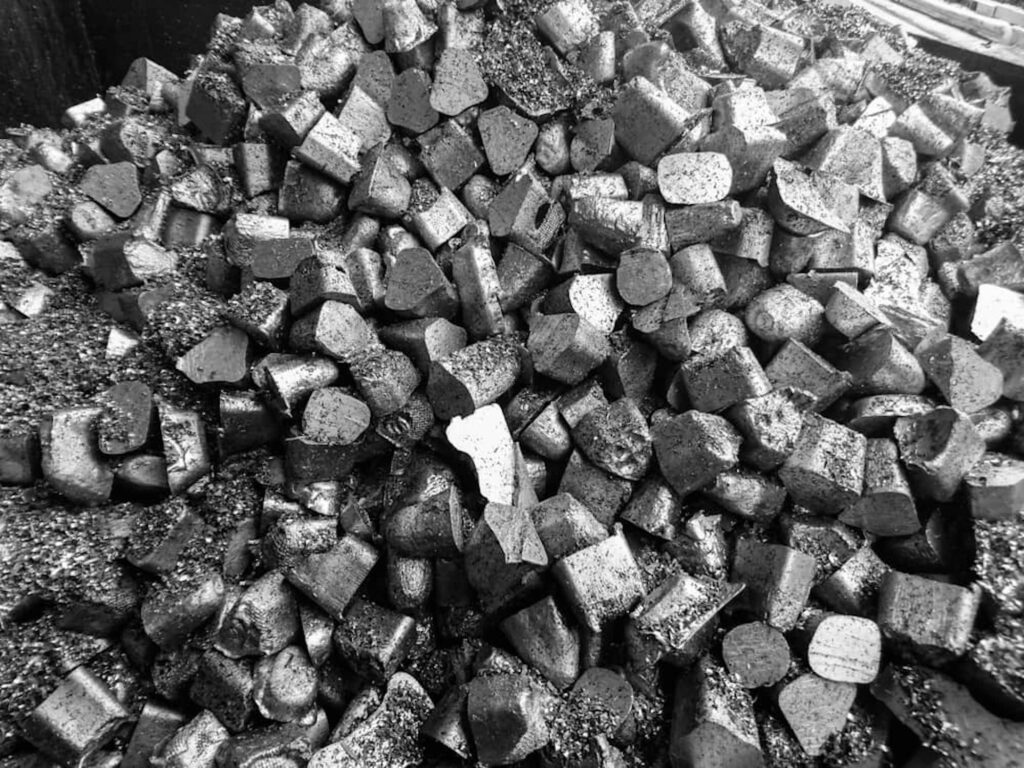
Al-Zn cast aluminum alloy
Chemical composition
Zinc (Zn) content: the main element, often added with silicon (Si) and magnesium (Mg) to form a strengthening phase.
Typical formulation: Al-Zn-Mg-Si, such as Al-8.33Si-0.36Mg-0.27Zn alloy.
Mechanical properties
Tensile strength (UTS): 164~214 MPa (lower in sand casting).
Heat treatment effect: The strength can be significantly improved after deterioration heat treatment.
Fields of application
Models & Tools: Pattern Plates, Equipment Brackets.
Medical devices: low-cost structural parts.
Advantages and disadvantages
Advantages: low price, can be used directly without heat treatment.
Disadvantages: high susceptibility to hot cracking and poor performance at high temperatures.
Special cast aluminium alloy
Al-Fe-RE alloy
Chemical composition: iron (Fe), rare earth (RE) such as Ce (0.4~0.5%), La (0.15~0.25%).
Performance: Excellent high temperature stability (working temperature up to 400°C), suitable for complex high temperature environment.
Application: Engine valves, aerospace high-temperature parts.
Rare earth reinforced aluminum alloy
Typical grade: ZL401 (including Y, Ce, Zr, etc.).
Mechanism of action: Rare earth refines grains, reduces gas inclusions, and improves fluidity and mechanical properties.
Application: New energy vehicle battery shell, large die-casting.
Heat-free aluminium alloy
Features: Avoid heat treatment deformation through component formula optimization.
Such as adding Sr, Sb, and are suitable for integrated die casting.
Applications: Tesla body structure, electric vehicle chassis.
The relationship between casting process and performance
Process selection
Sand casting: low cost, suitable for complex parts, but poor compactness.
Die-casting: suitable for thin-walled parts, but the tendency to crack (e.g. Al-Cu system) needs to be controlled.
Metal mold casting: increase the cooling rate and optimize the mechanical properties.
Performance-optimized paths
By adding rare earths (Ce, La), the grains are refined and defects reduced.
Additionally, T6 heat treatment (solution aging) enhances the material’s strength.
For instance, Al-Si-Mg alloy achieves an ultimate tensile strength (UTS) of 384 MPa after undergoing T6 treatment.