Gooseneck cost optimization,the gooseneck is the heart of a hot chamber die casting machine.
Where the molten metal is transported from the furnace to the mold cavity by bending a pipe (shaped like a gooseneck).
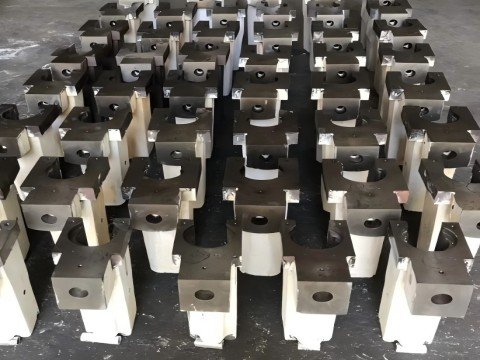
Its core functions include: metal flow control (to ensure smooth flow), high temperature/high pressure resistance.
To withstand high temperatures of 600-650°C and pressures of 10-70 MPa, and tightness assurance to prevent leakage.
Gooseneck cost structure
Material cost
High-quality cast steel, forged steel or special alloys (such as tungsten steel, silicon nitride ceramics) account for about 40-50%.
Precision casting, heat treatment (such as quenching, nitriding) and surface treatment (such as plating) account for 20-30%.
Maintenance & Replacemen
The frequency of replacements due to high-temperature corrosion has a direct impact on costs.
The life of ordinary gooseneck is about 1.5 million molds, and the inferior materials may be as low as 1 million molds, but after optimization, it can reach more than 2 million molds.
Energy costs
Nozzle heating (400-500°C) accounts for 15-20% of the total energy consumption of the equipment.
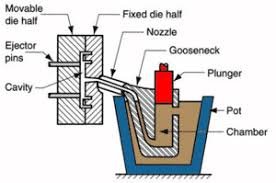
Gooseneck Cost Optimization
Material innovation and composite design
High-strength alloy substitution
By utilizing a composite structure of silicon nitride ceramics with temperature resistance exceeding 1200°C.
And tungsten steel, manufacturers have developed components that demonstrate 3-5 times greater longevity compared to traditional steel castings.
For example, the ceramic chamber is connected to the tungsten carbide barrel by a high-temperature adhesive to reduce metal residue and corrosion.
Gradient material technology
The inner layer consists of cemented carbide (such as WC-Co), while the outer layer comprises ductile steel, thereby achieving a balance between corrosion resistance and impact resistance.
Structural optimization and lightweighting
Fluid-Structure Interaction Simulation Optimization
After optimization, the weight of the gooseneck is reduced by 12%, and the manufacturing cost is reduced by 8%.
Modular design
The gooseneck is divided into detachable nozzle segments and connection segments, reducing the overall replacement cost (only the worn part needs to be replaced).
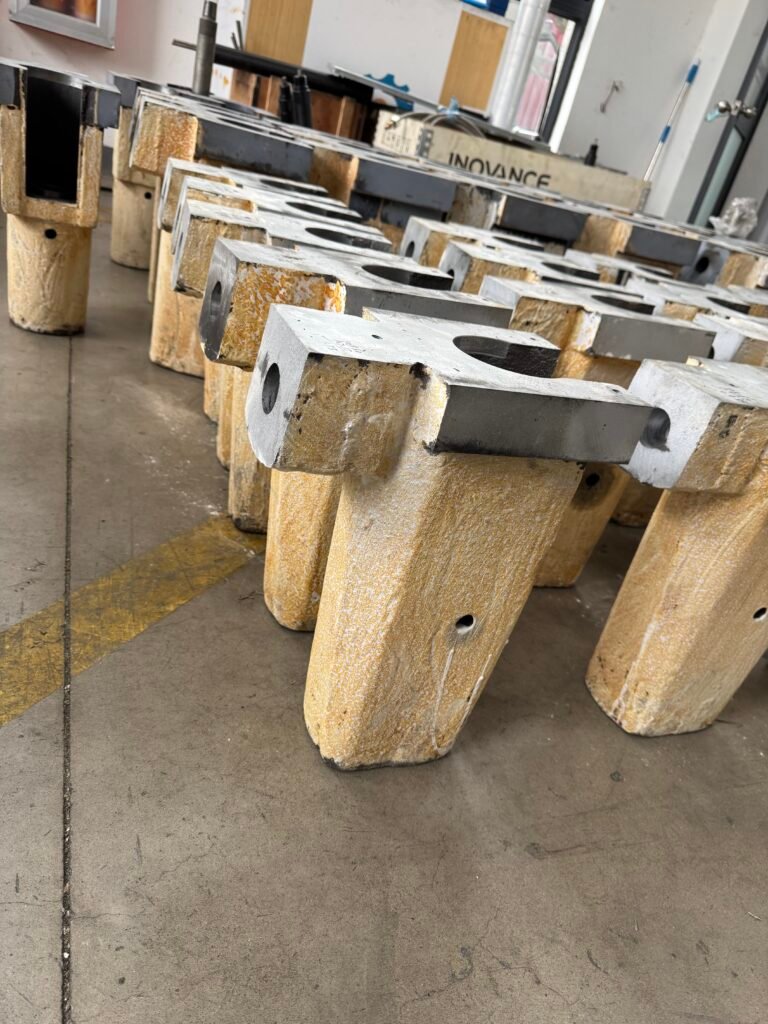
Intelligent control of process parameters
AI dynamic temperature adjustment
Real-time monitoring of gooseneck temperature through sensors, combined with machine learning to optimize heating power.
After application, energy consumption is reduced by 22% and temperature fluctuations are reduced from ±25°C to ±8°C.
Injection curve optimization
Increase the injection speed to 6-10 m/s (for magnesium alloys), shorten the setting time, and reduce the corrosion caused by metal retention in the gooseneck.
Maintenance strategy upgrade
Preventive maintenance system
Monitor gooseneck wear with vibration sensors to warn of replacement in advance and reduce unplanned downtime losses (60% reduction in failure rate).
Standardized spare parts management
Adopt a universal gooseneck design, adapt to multiple models, and reduce the cost of spare parts inventory.