In hot chamber die casting, the gooseneck is a critical component responsible for transferring molten metal and injecting it into the mold. Below are its key functions, structural features, and process-related details:
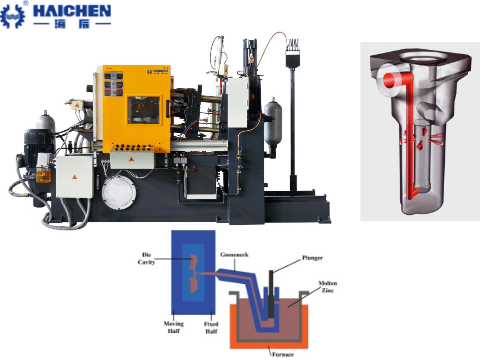
1. Core Functions & Design
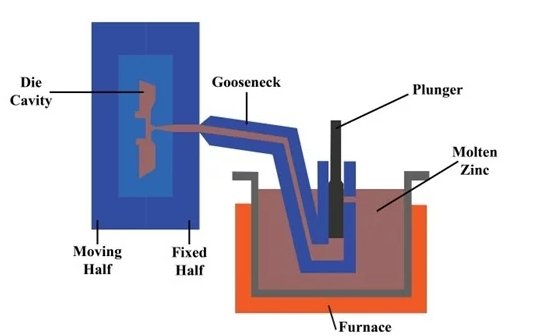
- Molten Metal Conduit: The gooseneck connects the molten metal reservoir (hot chamber) to the mold nozzle, forming a sealed flow path. Its internal channel design ensures rapid and smooth filling of the mold cavity.
- Injection Mechanism: In hot chamber machines, the gooseneck works with a hydraulic or pneumatic piston. The piston forces molten metal through the gooseneck into the mold and maintains pressure until solidification.
- Integrated Design: The gooseneck is typically submerged in molten metal to minimize heat loss and maintain fluidity. In some designs, the nozzle is heated to 400–500°C to prevent premature solidification.
2. Material & Thermal Resistance
- High-Temperature Materials: The gooseneck is made of heat-resistant alloys or cast iron to withstand repeated thermal shocks from low-melting-point metals (e.g., zinc, magnesium, lead).
- Thermal Deformation Control: Studies show that heat from molten metal can cause radial deformation in the gooseneck and pressure chamber, affecting piston alignment. Structural optimizations (e.g., reinforced supports, adjusted wall thickness) reduce deformation and improve reliability.
3. Process Compatibility
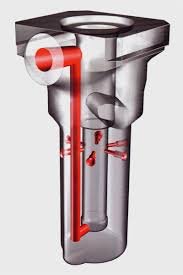
- Suitable Alloys: Hot chamber die casting and the gooseneck are designed for low-melting-point alloys (zinc, tin, lead, and some copper alloys), as their melting points (typically <450°C) do not damage the gooseneck.
- Unsuitable for Aluminum: Aluminum’s high melting point (~660°C) exceeds the gooseneck’s thermal limits, making cold chamber die casting necessary for aluminum parts.
4. Advantages & Challenges
- High Efficiency: Hot chamber processes have short cycle times (~15 cycles/minute), ideal for high-volume, small precision parts. The gooseneck’s integrated design enables faster metal injection.
- Maintenance & Costs: Regular maintenance is required to prevent metal residue buildup or corrosion. Material choice and structural design directly impact maintenance frequency and costs.
5. Workflow Example
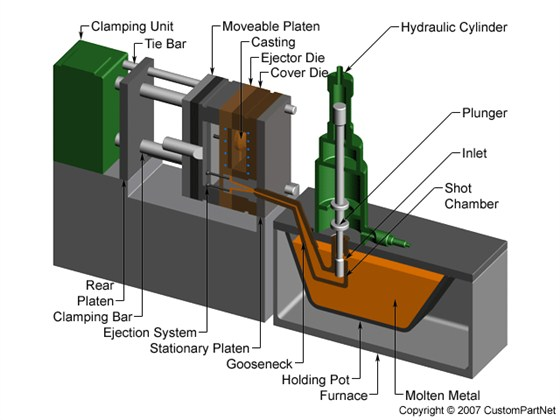
- Filling Phase: After mold closure, the piston retracts, drawing molten metal into the gooseneck via the feed port.
- Injection Phase: The piston advances, forcing metal through the gooseneck and nozzle into the mold cavity under high pressure until solidification.
- Reset & Ejection: The piston retracts, pulling excess metal back into the gooseneck. The mold opens, and the casting is ejected, completing the cycle.
6. Key Selection Criteria
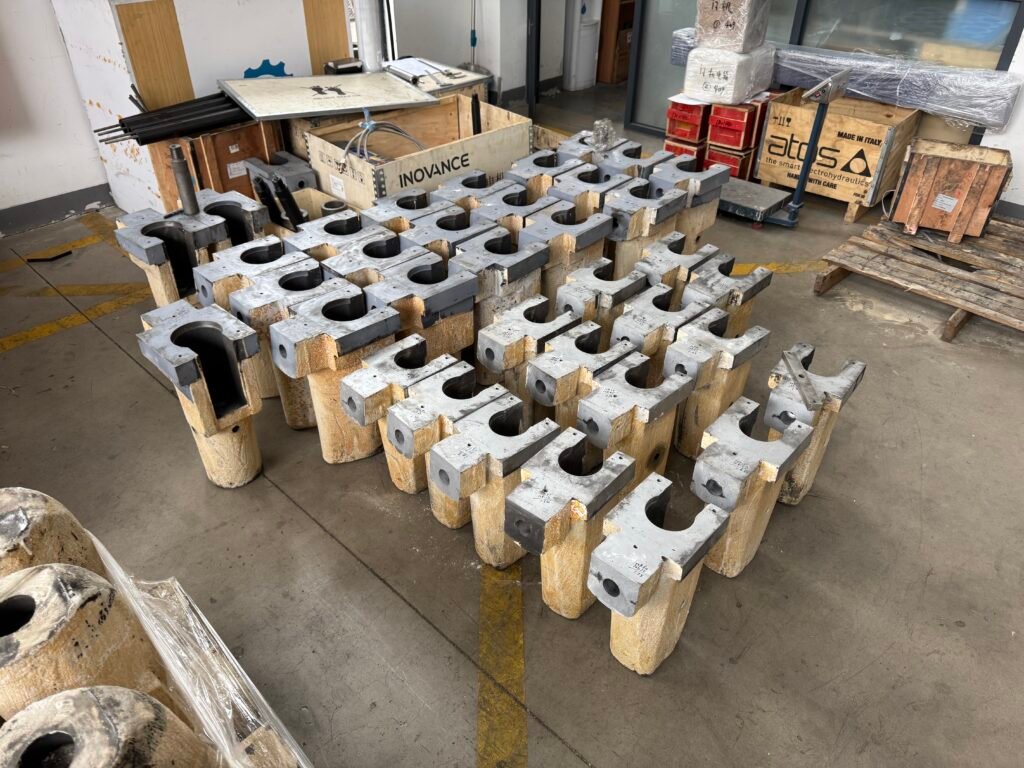
- Material Compatibility: Choose gooseneck materials (e.g., corrosion-resistant cast iron or coated alloys) based on the metal’s fluidity and corrosiveness.
- Temperature Control: Heating/cooling systems are essential to maintain optimal metal temperature during injection.
- Flow Optimization: Channel curvature, inner wall smoothness, and design minimize turbulence and oxidation.
The gooseneck is pivotal to hot chamber die casting, directly impacting productivity, part quality, and equipment lifespan. By optimizing materials, structure, and temperature control, its advantages for low-melting-point alloys are maximized while mitigating thermal deformation and corrosion risks. For high-melting-point metals like aluminum, cold chamber die casting remains the preferred method.
What is the gooseneck in die casting?
The gooseneck is a fundamental component in hot chamber die casting, a specialized process optimized for producing high-volume, precision parts from low-melting-point metals like zinc and lead. Below is a comprehensive breakdown of its definition, structure, functions, and operational significance:
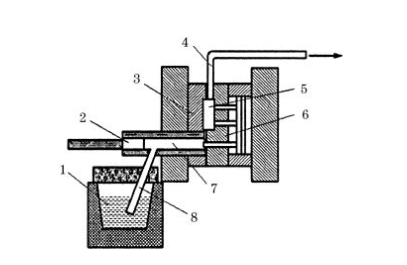
1. Definition and Core Role
The gooseneck is a curved metal conduit that bridges the molten metal reservoir (furnace) and the mold cavity in hot chamber die casting. It serves as the primary pathway for transferring molten metal under high pressure into the die, ensuring rapid and controlled filling of the mold . Its name derives from its resemblance to the curved neck of a goose .
2. Structural Design and Materials
Key Components
- Curved Tube: Engineered to minimize turbulence and ensure smooth metal flow .
- Nozzle: The outlet end that interfaces with the mold’s sprue, directing molten metal into the cavity .
- Cylindrical Lining: Houses the plunger/piston and maintains precise alignment during injection .
- Replaceable Parts: Designed for easy replacement due to wear from high-temperature and high-pressure cycles .
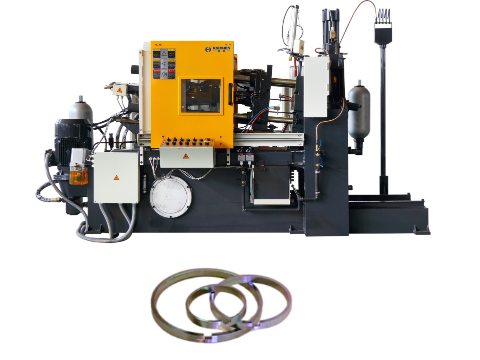
Material Selection
- High-Temperature Alloys: Typically made from cast iron, tool steel, or nickel-based alloys to withstand prolonged exposure to molten metal (400–500°C) and resist thermal degradation .
- Thermal Resilience: Materials are chosen to minimize radial deformation caused by thermal expansion, which could disrupt piston alignment .
3. Functional Workflow in Hot Chamber Die Casting
The gooseneck is central to the four-stage cycle of hot chamber die casting:
- Filling Phase:
- The gooseneck is submerged in the molten metal bath. As the plunger retracts, metal flows into the gooseneck via gravity or inlet ports .
- Continuous heating maintains fluidity and prevents premature solidification .
- Injection Phase:
- A hydraulic or pneumatic plunger forces molten metal through the gooseneck and nozzle into the mold cavity at pressures ranging from 10–70 MPa (1,450–10,000 psi) .
- The curved design ensures laminar flow, reducing oxidation and turbulence .
- Solidification and Reset:
- Pressure is maintained until the metal solidifies. The plunger then retracts, pulling excess metal back into the gooseneck .
- Ejection and Cycle Repeat:
- The mold opens, ejector pins release the casting, and the gooseneck refills for the next cycle .
- The mold opens, ejector pins release the casting, and the gooseneck refills for the next cycle .
4. Advantages of Gooseneck Design
- High Efficiency: Enables rapid cycling (up to 15–60 shots/minute) for mass production of small to medium parts .
- Thermal Integration: Submersion in molten metal minimizes heat loss, ensuring consistent metal viscosity .
- Precision: Optimized geometry ensures uniform filling of complex molds, producing parts with tight tolerances and smooth surfaces .
5. Limitations and Maintenance Challenges
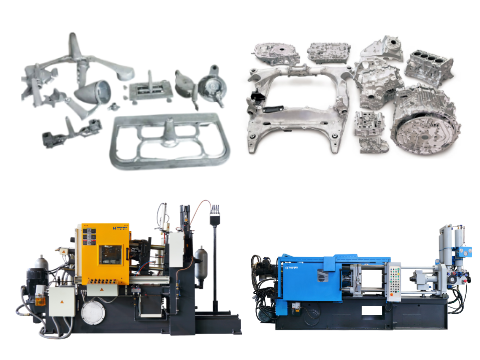
- Material Constraints: Suitable only for low-melting-point alloys (e.g., zinc, magnesium). Aluminum (melting point ~660°C) exceeds thermal limits, necessitating cold chamber systems .
- Wear and Corrosion: Prolonged exposure to molten metal and high-pressure cycles causes gradual degradation, requiring periodic replacement of gooseneck components .
- Maintenance Costs: High-quality materials and precision machining increase initial and upkeep expenses .
6. Comparison to Cold Chamber Systems
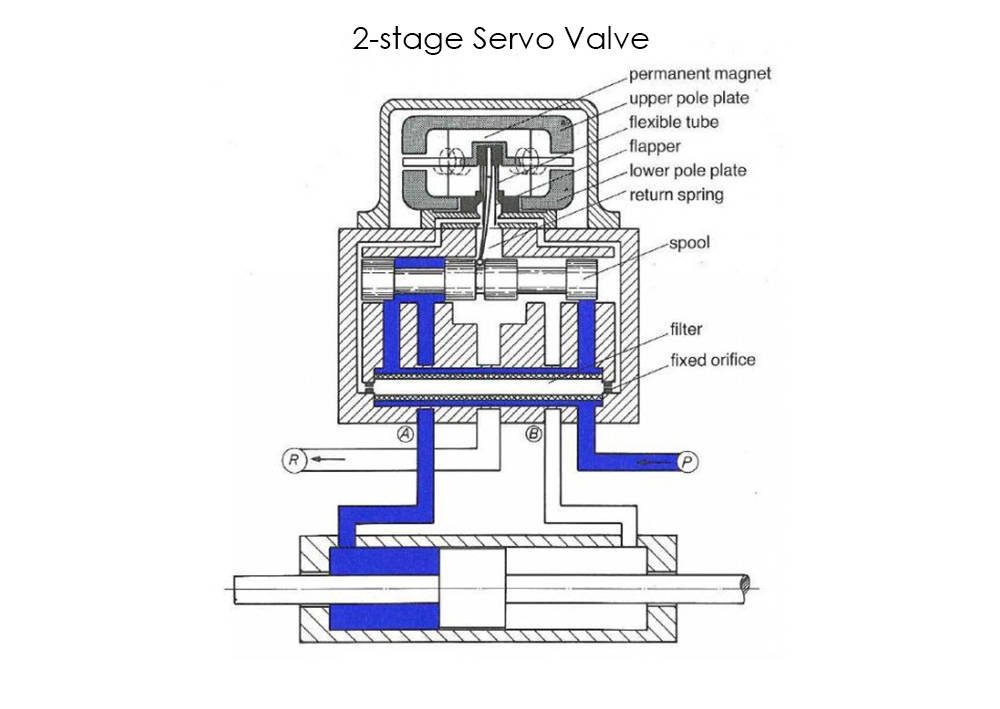
Feature | Hot Chamber (Gooseneck) | Cold Chamber |
---|---|---|
Metal Transfer | Direct submersion in molten metal reservoir | Ladle-fed; no direct furnace connection |
Pressure Range | 10–70 MPa | 35–140 MPa |
Suitable Metals | Zinc, magnesium, lead | Aluminum, copper alloys |
Cycle Speed | Faster (15–60 cycles/minute) | Slower (due to manual metal transfer) |
Component Wear | Higher (due to thermal exposure) | Lower |
7. Industrial Applications
The gooseneck’s efficiency makes it ideal for producing:
- Consumer Electronics: Zinc alloy connectors, housings.
- Automotive Parts: Magnesium gearbox components, fuel system parts.
- Hardware: Precision fasteners, plumbing fixtures .
8. Innovations and Optimizations
- Enhanced Coatings: Thermal barrier coatings (e.g., ceramic) to extend component lifespan .
- Modular Design: Quick-swap gooseneck systems to reduce downtime during maintenance .
- Simulation Tools: CFD modeling to optimize gooseneck geometry for reduced turbulence .
Conclusion
The gooseneck is the linchpin of hot chamber die casting, enabling high-speed, precision manufacturing of low-melting-point alloy components. Its design balances thermal resilience, hydraulic efficiency, and operational durability, though material limitations and maintenance demands necessitate careful process planning. For industries prioritizing volume and precision in zinc or magnesium parts, the gooseneck remains indispensable, while alternative methods like cold chamber casting address higher-temperature alloy needs .
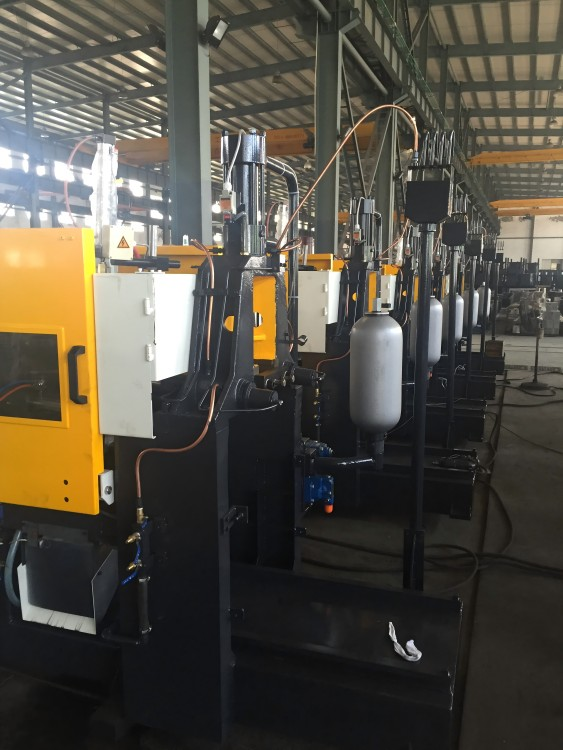
As a professional hot chamber die casting machine manufacturer, Haichen has rich experience in die casting gooseneck kettles.
You are welcome to contact us at any time.