The processes of Hot Chamber Die Casting Work encompasses the stages of melting the metal, injecting it into the die, cooling it, and getting the part out of the die.
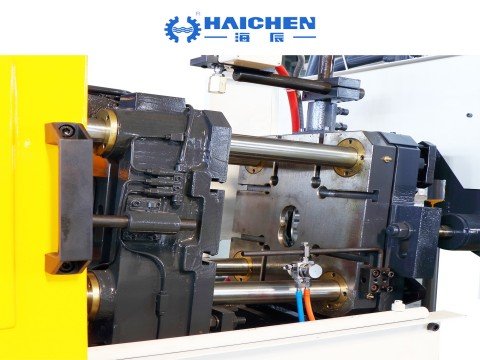
The hot chamber die casting work process is most efficient for producing intricate details in high pressure applications. Which makes it great for producing complex metal parts.
Casting components from zinc, aluminum, and magnesium alloys are commonly done using this method.
Melting the Metal
The metal is melted in a furnace for hot chamber die casting.
To avoid cooling, we have to keep the molten metal in a heated chamber reserves till an optimal casting temperature is reached.
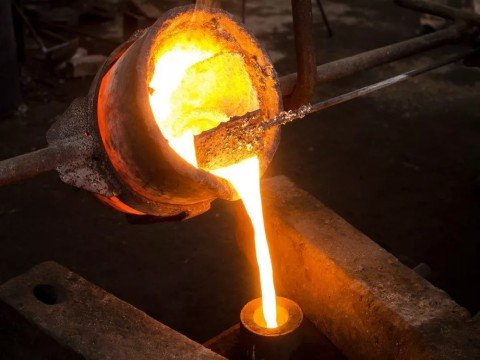
Injecting the Metal
Once heated, we can inject the molten metal into a mold under high pressure.
To inject the metal, a plunger or piston pushes it from the heated chamber into the mold.
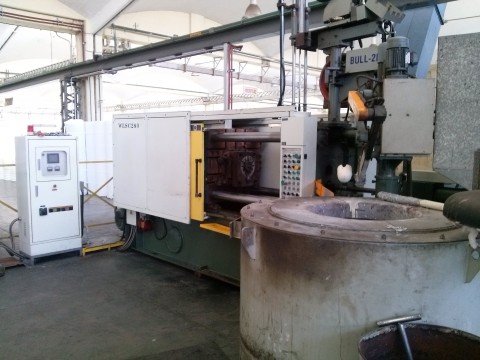
Hot chamber die casting work-Casting the Part
Now, the desired part must be made by melting the metals directly into the molds. With hot cavity die casting maintained with high pressure. Above all, this is The desired part is achieved by the modified hot chamber die casting. Where the metals are melted directly into the molds and kept under high pressure. Each step must be done carefully.

When the cast is complete, it undergoes cooling and solidification.
The procedure ensures that all details are retained within the mold which will result in a smooth-surfaced part. It is also important to ensure that there is insufficient gas left within the space to guarantee that it can drive the air out of the chamber for filling all section with metal.
Final Cooling
We require the space within the cooling region to be sealed during the initial cooling stage since it will lead to an increase in strength and durability.

Part Ejection
The ejection process is done once the given part has entirely cooled and solidified in the mold. The subsequent processes include removal of flash and excess material. Therefore,which will be succeeded by cleaning, polishing, or finishing as required.
Post-Processing
To comply with the desired specifications. Further operations such as trimming, gouging, or even painting may be employed to the components depending on their designated application.
HAICHEN: Manufacturer of Hot Chamber Die Casting Machines
HAICHEN, on the other hand, is a hot chamber die casting machines manufacturer with a reputation of precision, efficiency and reliability.
We ensure our machines withstand complications of high-pressure casting. So that each part we put our effort into is guaranteed to be of the finest quality.
Due to persistent efforts in coming up with modern solutions such as those which aid in the automotive and consumer electronics components, HAICHEN has become an undisputed leader in the die casting industry.
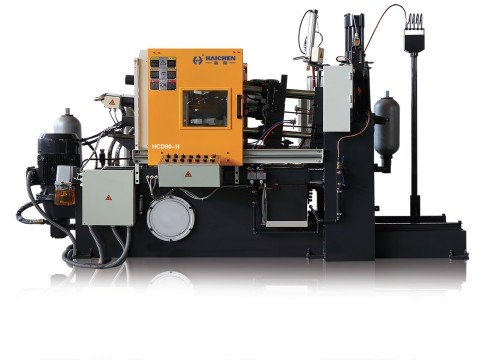
In conclusion,we understand the distinction hot chamber die casting provides for its precision, efficiency and ability to produce complex parts with thin walls and minute details.
Its widespread application in automotive, consumer goods, and electronics further highlights its importance in manufacturing a multitude of components.