In the die casting process, the importance of the material in die casting is that it directly affects the quality, performance, and production cost of the casting.
In the die casting process, different materials have different performance characteristics. It directly affect the quality of die-casting parts, production efficiency, and the application areas of the final products.F
First of all, non-ferrous metals such as aluminum, zinc, and copper alloys are commonly used in die casting. Because these materials have a lower melting point and are suitable for injection into molds under high pressure.
These materials not only provide good mechanical properties but also enable high precision and complex geometries.
The important position of die casting material
Die casting materials have an extremely important position in die casting. The choice of die casting materials directly affects the quality and performance of die castings.
For example, aluminum alloy has become one of the most widely used die-casting materials due to its advantages of low density, high specific strength, good thermal conductivity and strong corrosion resistance. And it is widely used in automobiles, motorcycles, aerospace and other fields.
In addition, magnesium alloys are also favored in the context of automotive light weighting. Because the light weight, high strength and good plasticity.
The selection and optimization of die casting materials not only affects product quality and production efficiency. But also has great significance for environmental protection and sustainable development.
Light metal materials such as aluminum alloy and magnesium alloy have the advantages of recyclability and reuse. And meet the requirements of energy conservation and environmental protection in modern manufacturing industry.
Die casting materials play a vital role in modern manufacturing, not only affecting the quality and performance of products. But also related to the realization of sustainable development and environmental protection goals of the industry.
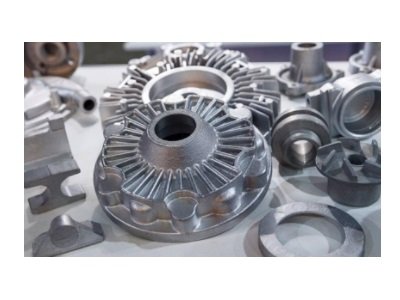
How to choose important materials for casting
In the die casting process, the choice of material is crucial. Because it directly affects the performance, quality, and production cost of the final product.
Here is a detailed analysis of the importance of materials in die casting:
The mechanical properties of die casting materials
Such as strength, hardness, and corrosion resistance, are key factors in determining the performance of a product.
For example, aluminum, zinc and copper alloys are often used in the die casting process. Due to the low melting point and good mechanical properties.
These materials are not only able to withstand high-pressure injection, but also provide high surface finish and dimensional accuracy.
Melting point and thermal behavior
The melting point and thermal behavior of a material have a significant impact on the mould design and production process.
Die casting moulds are typically made of tool steel with high hardness and high temperature resistance to withstand high temperature and high pressure environments.
For example, die-casting moulds for aluminum, magnesium, and zinc alloys require the use of high-quality H13 tool steel. It can ensure mould life and product quality.
Cost-benefit analysis
The choice of materials also involves a cost-benefit analysis. For high-volume production, die casting is a cost-effective process because it reduces the need for post-processing and increases productivity.
However, for low-volume production, the high fixed cost of the mould can make die casting uneconomical. Therefore, when choosing a material, its cost-benefit ratio must be taken into account.
Different application scenarios
Different die casting materials are suitable for different application scenarios. For example, aluminum and zinc alloys are often used in the manufacture of large and small die castings due to their low cost and good flowability.
Whereas, copper alloys are suitable for applications that require higher strength and corrosion resistance due to their higher melting point and mechanical properties.
Environmental impact
The choice of materials should also take into account their environmental impact. For example, cadmium contained in zinc alloys needs to be separated and treated through a specific process to reduce environmental hazards.
Therefore, when choosing a die casting material, its environmental performance should be considered.
The processability of the material is also an important basis for selection. Die casting materials need to have good casting properties in order to smoothly fill the mould under high pressure and form high-quality castings.
For example, aluminum alloys have good casting properties and are suitable for manufacturing parts with complex shapes.

The importance of improving the formulation of casting materials
Haichen has improved its die casting material formulations to improve production efficiency and reduce costs by taking the following approaches:
Optimizing material ratios: By changing the proportions of different materials and adding other metal elements, Haichen can improve the physical and chemical properties of materials.
For example, adding small amounts of silicon and magnesium to aluminum alloys can improve the strength and toughness of the material.
Use magnesium alloys: Magnesium alloys have lower production costs when produced in large quantities because their mould life is typically 2 to 3 times longer than that of aluminum alloys.
In addition, magnesium alloys can improve the metallurgical density and mechanical properties of parts through processes such as vacuum die casting, oxygenated die casting, semi-solid die casting and high-pressure die casting.
Haichen adopts integrated die-casting technology: the integrated die-casting mode highly integrates multiple parts, which reduces the construction cost of the production line, the improvement of material utilization rate and the reduction of labor cost.
At the same time, the process flow is simplified and the production efficiency is significantly improved.
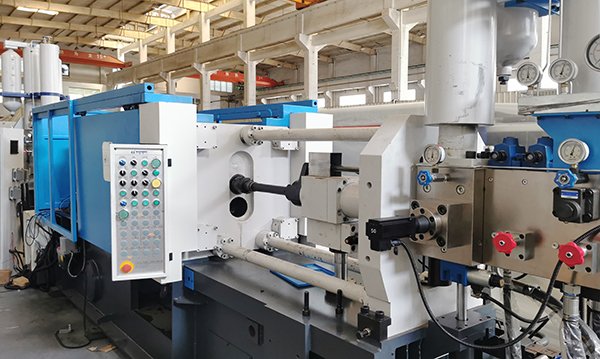