Smart Boosting Handwheel is a high-precision operating device that integrates sensors, wireless communication, and real-time control algorithms.
And is mainly used for the precise adjustment of key parameters (e.g., injection speed, pressure, and clamping force) in die casting systems.
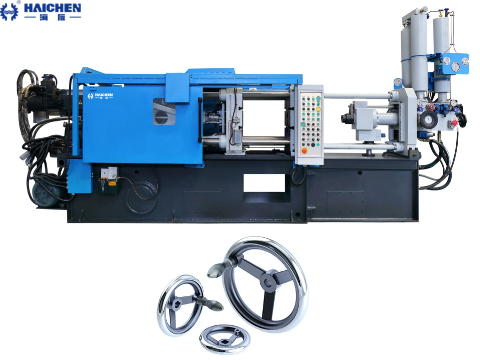
Smart boosting handwheel in die casting Systems
Dynamic feedback control
Real-time data collection through pressure and position sensors, combined with closed-loop control algorithms to automatically adjust the actuator.
Such as motor or hydraulic valve to ensure the stability of process parameters.
Wireless operation and multi-axis control
Wireless transmission technology, such as the HR 550 FS handwheel from HEIDENHAIN.
Enables multi-axis selection and remote operation, reducing cable constraints and increasing operational flexibility.
Safety Enhancements
Integrated E-STOP button, low voltage alarm, and vibration alert function to ensure safe operation.
Specific application scenarios in die casting systems
Injection speed and pressure regulation
During the die casting process, the smart handwheel dynamically controls the injection punch’s speed and pressure profile, thereby enabling real-time optimization of the casting cycle.
For example, Yizumi’s LEAP9000T die-casting machine realizes 10 speed stages (0.05~12m/s) adjustment through a handwheel.
And uses the end brake function to reduce flash and improve the quality of castings.
Low-speed stage (50~700mm/s): Fine-tuning of the handwheel ensures that the molten metal fills the cavity smoothly and avoids porosity.
High-speed phase (>8 m/s): Efficient filling of thin-walled parts with fast response (acceleration time < 20 ms).
Dynamic optimization of clamping force
The intelligent handwheel is linked with the real-time monitoring system, which can dynamically adjust the clamping force.
For example, a high-end foundry project in Shanghai used an intelligent injection system to increase the clamping speed by 7% and shorten the production cycle.
Mold adjustment and maintenance
During the mold change process, the handwheel is used to precisely adjust the force on the corins to avoid overloading.
For example, the IMPRESS-PLUS die casting machine’s intelligent mold adjustment system automatically calibrates the clamping force to a set value, reducing the mold change time to less than 1 hour.
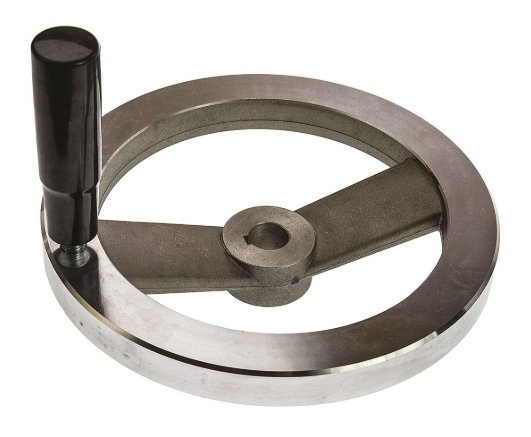
The technical principle of the intelligent supercharged handwheel
The intelligent supercharged handwheel is a new type of actuator that integrates mechanical transmission and digital control.
Signal Conversion System
Incremental encoder (2000 lines/turn) is used to convert the rotation angle of the handwheel into a pulse signal with a resolution of up to 0.1° .
Built-in Hall sensor to detect torque (0-5Nm adjustable) to achieve pressure-speed coupling control.
Closed-loop control mechanism
The pulse signal is received through the PLC to adjust the proportional valve opening in real time.
Then, the pressure sensor feeds back the actual pressure increase value (accuracy ± 0.2MPa) to form a PID control closed loop.
Human-computer interaction innovation
The LCD display integrates axis coordinate display (resolution 1μm) and magnification switching (×1/×10/×100).
The safety locking design incorporates a dual independent locking system to prevent false touch,additionally, the user must press the enabling switch to activate the operation.
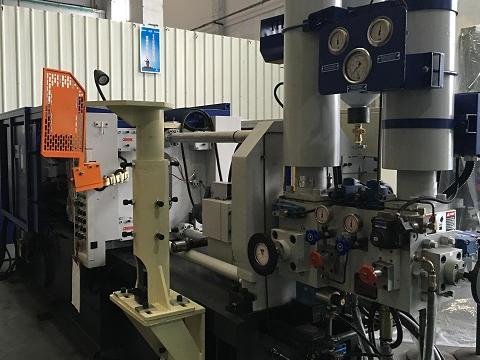
Technology Development
Trend AI Fusion: Predict the best boost curve through machine learning algorithms, such as the real-time casting defect prediction system adopted by Tesla Giga Press.
Haptic feedback: Introduce force feedback motors (such as HD haptic technology) to simulate the flow resistance of different molten metals.
Modular design: quick-change pressurized module supports magnesium/aluminum alloy process switching.