The die casting operation steps involve preparing the mold, heating metal, injecting it into the mold, cooling, ejecting the part, post-processing, etc.
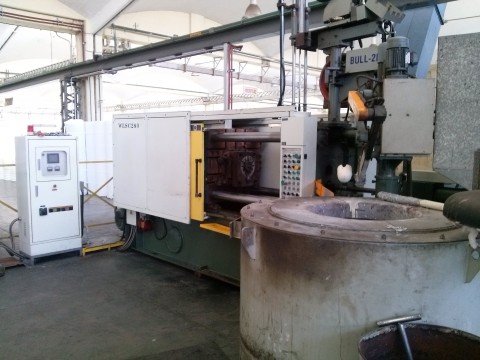
Die casting can produce precision parts made from a wide range of materials, including aluminum alloys, zinc alloys, and copper alloys.
Die Casting Process Steps: A Step-by-Step Guide
The die casting operation follows a precise sequence to ensure high-quality metal parts. Here’s a breakdown of the high pressure die casting process step by step:
Mold Preparation – The die (mold) is cleaned and lubricated to prevent sticking.
Injection – Molten metal is forced into the mold under high pressure.
Cooling – The metal solidifies inside the die.
Ejection – The casting is removed using an extractor or ejector pins.
Finishing – Excess material (flash) is trimmed, and the part is inspected.
Each step in the die casting machine process is critical for efficiency and part quality. Understanding these die casting process steps helps optimize production and reduce defects.
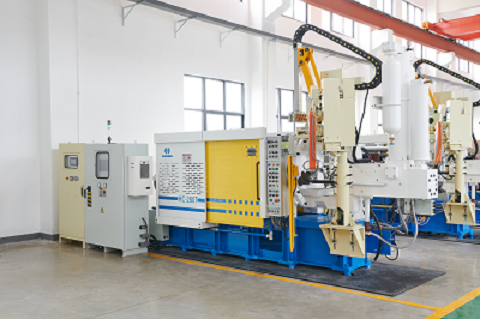
Die casting operation steps
- Preparing the Die Cavity
- Die casting operation steps-Heating the Metal
- Injecting the Molten Metal
- Cooling and Solidification
- Die casting operation steps-Ejection of the Casting
- Post-processing
- Inspection and quality control
- Finishing touches
1. Preparing the Die Cavity
The first step in die casting is to prepare the die cavity. This involves creating a die with two or more parts that will form the shape of the final product. The mold needs to withstand high pressure and high temperature.
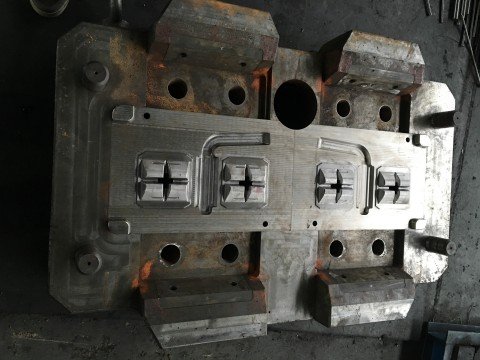
2. Die casting operation steps-Heating the Metal
Workers heat metal billets or ingots to their melting points, reaching 650-700°C (1202-1292°F) for aluminum alloys, then prepare the molten metal for die injection.
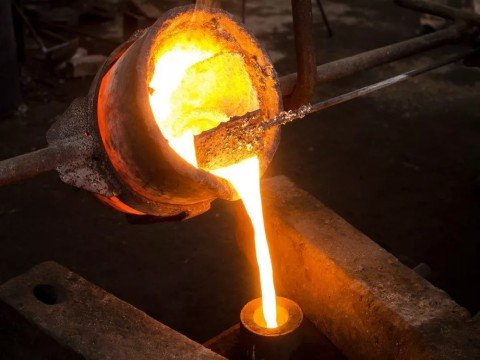
3. Injecting the Molten Metal
The molten metal is injecting into the die cavity under high pressure, usually using a hydraulic or mechanical system. The pressure ensures that the metal completely and evenly fills the die.
4. Cooling and Solidification
Once the die is filled, the metal begins to cool and solidify. This process is critical to achieving the desired shape and mechanical properties.
5. Die casting operation steps-Ejection of the Casting
Once the metal has solidified, the die opens and the die casting ejection system removes the finished product from the die. This step may also involve removing any excess material or burrs.
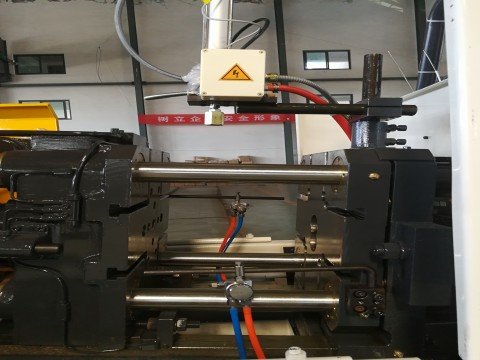
6. Post-processing
Die castings may require post-processing operations such as trimming, deburring or polishing to achieve the desired appearance and remove any defects.
7. Inspection and quality control
Finally, the finished die castings undergo inspection and quality control to ensure that they meet the required specifications and standards.
8. Finishing touches
Depending on the application requirements, die castings may receive additional treatments such as painting, plating or anodizing to enhance their appearance or performance.
Quality Control and Inspection
Real-Time Monitoring
- Using sensors and automated systems to monitor the production process: Sensors and automated systems installed on the production line can monitor key parameters in the die casting process, such as temperature, pressure, and injection speed. These systems can automatically record data and generate reports to help operators keep track of the production status.
- Detecting and correcting deviations in a timely manner: Real-time monitoring systems can quickly detect any deviations in the production process, such as abnormal temperatures or insufficient injection pressure. Once a deviation is detected, the system will immediately issue an alarm, allowing operators to take swift action to adjust and ensure the stability and consistency of the production process.
Finished Product Inspection
- Checking part dimensions and surface quality: Using high-precision measuring tools (such as coordinate measuring machines) to check the dimensional accuracy of parts to ensure they meet design requirements. At the same time, assess the surface quality of parts through visual inspection and surface roughness instruments, checking for defects such as scratches, porosity, and shrinkage.
- Performing non-destructive testing (such as X-ray, ultrasonic testing): For some critical parts, non-destructive testing techniques (such as X-ray testing, ultrasonic testing) are used to inspect internal structures and potential defects. These testing methods can accurately detect internal cracks, porosity, inclusions, and other defects without damaging the parts, ensuring the mechanical properties and reliability of the parts.
- Ensuring parts meet design specifications and quality standards: All inspection and testing results will be compared with design specifications and quality standards to ensure that each part meets the requirements. Parts that do not meet the standards will be reworked or scrapped to ensure the quality of the final product.
Common Issues and Solutions
Porosity and Shrinkage
- Cause Analysis (such as injection speed, mold temperature): Porosity and shrinkage are common defects in the die casting process. Porosity is usually caused by too fast injection speed or poor mold venting, while shrinkage may be due to too high mold temperature or uneven cooling speed. Additionally, excessive gas content in the molten metal can also lead to porosity.
- Solutions (optimizing injection parameters, improving mold design): To reduce the occurrence of porosity and shrinkage, injection parameters can be optimized. Such as reducing injection speed, adjusting injection pressure, and holding time. At the same time, improve mold design by adding venting channels. And optimizing the cooling system to ensure uniform mold temperature distribution. Additionally, vacuum die casting technology can be used to reduce the gas content in the molten metal.
Surface Defects
- Cause Analysis (such as mold wear, improper lubrication): Surface defects such as scratches, pitting, and uneven gloss are usually caused by mold wear. Improper lubrication, or poor mold surface treatment. Minor defects or uneven lubricant distribution on the mold surface can lead to a decline in part surface quality.
- Solutions (regular mold maintenance, adjusting lubricants): Regularly inspect and maintain the mold, promptly repair wear and scratches on the mold surface. Use high-quality mold lubricants and ensure even distribution of the lubricant. Additionally, regular surface treatment of the mold, such as polishing and coating, can improve part surface quality.
Insufficient Mechanical Properties
- Cause Analysis (such as material selection, cooling speed): Insufficient mechanical properties may be due to improper material selection, too fast or too slow cooling speed. Or unreasonable injection parameters. The chemical composition and physical properties of the material have a direct impact on the mechanical properties of the part, while cooling speed and injection parameters affect the microstructure and properties of the part.
- Solutions (optimizing material formulation, adjusting cooling time): Choose the appropriate material formulation to ensure that the chemical composition. And physical properties of the material meet the design requirements. Adjust cooling time and injection parameters to optimize the microstructure of the part and improve its mechanical properties. Additionally, post-treatment processes such as heat treatment can further improve the strength and toughness of the part.
Haichen Machinery – China’s die casting machine manufacturer
Haichen Machinery specializes in producing state-of-the-art die casting machines that are precise, durable and efficient.
Our quality system ensures each production stage – from mold setup to final ejection – meets rigorous quality benchmarks.
Haichen’s die casting machines Provides advanced control systems that help achieve optimal performance.
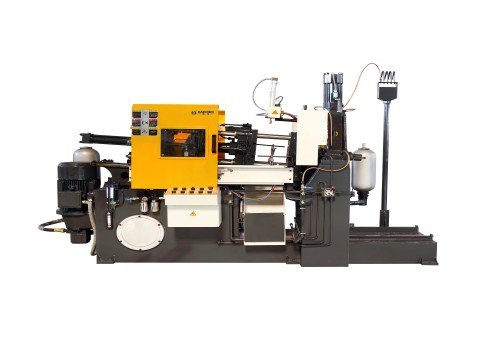
Die casting operations are a complex process that combines precision engineering and high-pressure technology to efficiently produce high-quality parts.
Understanding the die casting operation steps can help manufacturers optimize their processes and produce parts that meet the highest quality and performance standards.