The structure and principle of crankcase die casting machines feature key components like the injection system, mold clamping, melt handling.
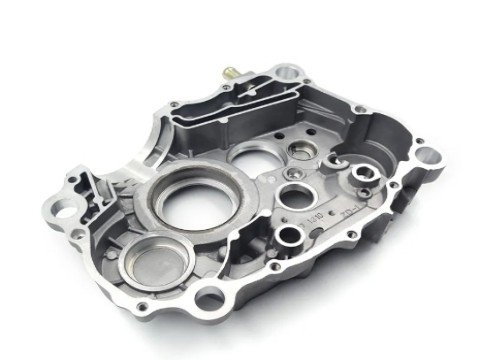
Crankcase die casting machines specialize in producing high-precision, complex metal parts like engine crankcases through the die casting process.
These machines combine advanced technology with robust engineering to ensure high-quality production.
In this article, we will explore the structure and working principle of crankcase die casting machines.
Structure of Crankcase Die Casting Machine
Injection System
The injection system is the core component of a crankcase die casting machine. It includes the injection cylinder, plunger, and nozzle. The primary function of this system is to inject molten metal into the mold cavity at high speed and pressure. The injection cylinder controls the movement of the plunger, which forces the molten metal through the nozzle and into the mold.
Mold Clamping System
The mold clamping system holds the mold halves together during the injection process. It consists of clamping plates, tie bars, and a toggle mechanism. The clamping force must be sufficient to withstand the injection pressure and prevent the mold from opening. The toggle mechanism provides the necessary mechanical advantage to generate high clamping forces.
Melt Handling System
This system is responsible for melting and maintaining the metal at the appropriate temperature. It includes a melting furnace, holding furnace, and transfer mechanism. The melting furnace heats the metal to its melting point, and the holding furnace maintains a consistent temperature until injection into the mold.
Ejection System
The ejection system removes the finished part from the mold. It consists of ejector pins, plates, and a drive mechanism. Once the metal solidifies, the ejector pins push the part out of the mold cavity, readying it for removal and preparation for the next cycle.
Control System
The control system manages the entire die casting process. It includes sensors, controllers, and a user interface. The control system ensures precise regulation of injection speed, pressure, mold temperature, and other parameters. Advanced control systems can also monitor and adjust the process in real-time to maintain consistent quality.
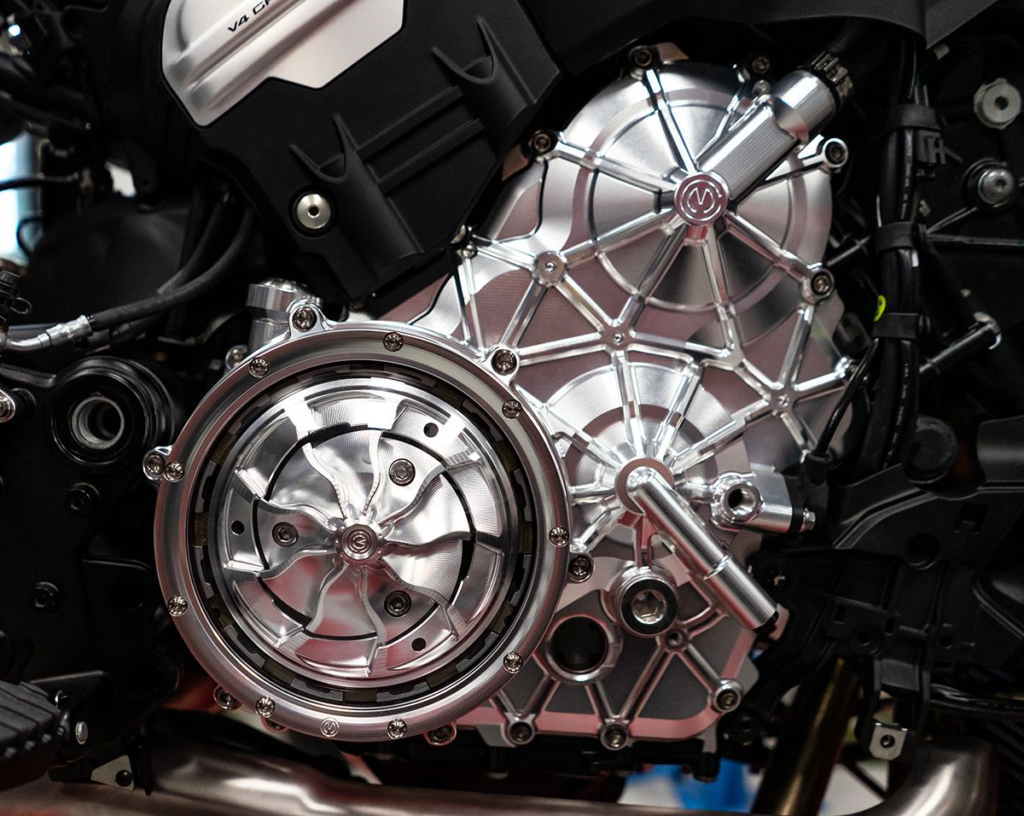
Principle of Crankcase Die Casting Machine
Preparation
The process begins with the preparation of the mold. Clean and coat the mold halves with a release agent to prevent the metal from sticking, then close and securely clamp the mold.
Injection
Molten metal is transferred from the holding furnace to the injection cylinder. The plunger moves forward, injecting the molten metal into the mold cavity at high speed and pressure. The metal fills the cavity rapidly, ensuring a precise replication of the mold design.
Solidification
Once the metal is injected, it begins to cool and solidify. The mold remains closed until the part has fully solidified. The cooling process carefully controls the solidification to ensure uniformity and prevent defects.
Ejection
After solidification, the mold opens, and the ejection system pushes the finished part out of the mold. The operator then removes the part, inspects it, and prepares it for further processing or packaging.
Cycle Repeat
Operators clean, coat, and close the mold again, repeating the process. The entire cycle is highly automated, enabling high production rates and consistent part quality.
Haichen: China’s famous die-casting machine manufacturer
HAICHEN is a leading manufacturer of die casting machines, known for its advanced technology and high-quality products. HAICHEN’s crankcase die casting machines are designed to deliver exceptional precision, efficiency, and reliability. Key features include:
- Advanced Control Systems: HAICHEN machines are equipped with state-of-the-art control systems that ensure precise regulation of the die casting process.
- Energy Efficiency: HAICHEN’s machines incorporate energy-saving technologies to reduce operational costs and environmental impact.
- Automation: HAICHEN machines often feature automated systems for mold handling, injection, and ejection, enhancing productivity and reducing labor costs.
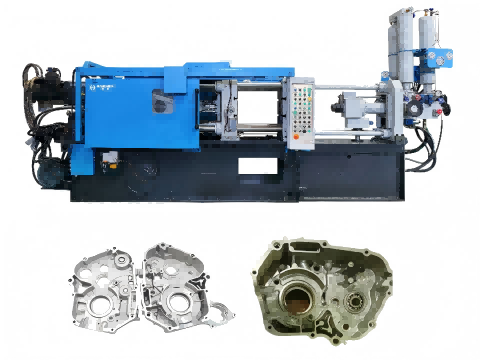
Crankcase die casting machines are essential tools in the production of high-precision metal parts. Structure and principle of crankcase die casting machine ensure consistent quality and high production rates.