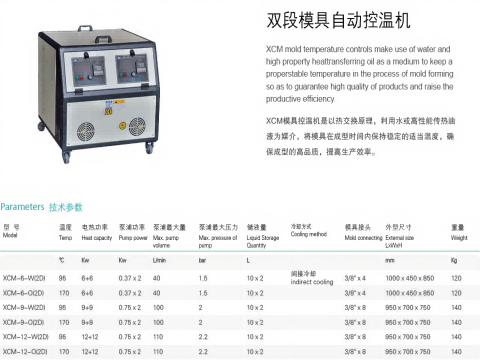
The Mold Temperature Controller in die casting is mainly used to control the mold temperature, ensure the stability of the die casting process, and improve the casting quality and mold life.
The working principle of the die casting mold temperature controller is to heat or cool the mold by circulating a heat transfer medium (oil or water) to form a closed-loop system.
Reasonable selection and operation of die-casting mold temperature controller is the key to improving the yield of die-casting parts and reducing production costs. It needs to be finely configured in combination with process requirements and equipment characteristics.
Are there still many questions about die casting cooling technology?Let’s make it clear for you .
1. Water-Cooled Mold Temperature Controllers
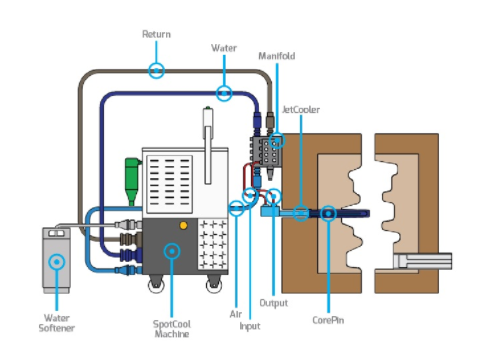
- Principle: Use water as the cooling medium, circulating through internal cooling channels to remove heat. Water offers high thermal conductivity and low cost, suitable for medium-low temperature control (e.g., 200–250°C for aluminum alloy molds).
- Applications: Common for zinc alloy (160–200°C) and magnesium alloy (180–240°C) die casting. Closed-loop control via smart systems (e.g., thermocouple monitoring with automatic valve adjustment).
- Advanced Designs: Combine 3D-printed inserts with high-pressure cooling systems for localized rapid cooling in complex molds.
2. Oil-Cooled Mold Temperature Controllers
- Principle: Use high-temperature thermal oil as the medium for heating/cooling. Oil’s high specific heat capacity suits high-temperature needs (e.g., 280–350°C for copper alloys), with ±5°C precision.
- Advantages: Uniform heating and reduced thermal shock. Example: Austria’s Robamat oil heaters use microcomputer control, operate at 350°C, and include dual overheat protection and oil-level monitoring.
- Applications: Ideal for large aluminum/magnesium alloy molds or scenarios requiring precise thermal balance.
3. Air-Cooled Mold Temperature Controllers
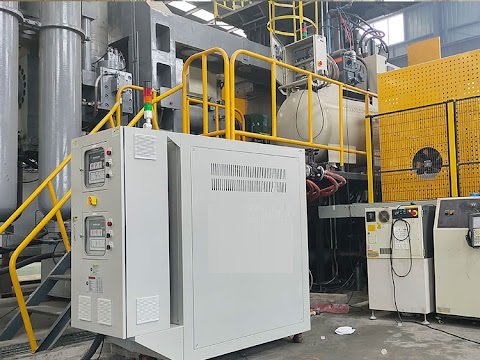
- Principle: Use forced air convection (e.g., fans) for cooling. Lower efficiency than water/oil but cost-effective for simple molds or auxiliary cooling.
- Limitations: Limited precision, typically used for small molds or parts tolerant to temperature fluctuations.
4. Integrated Temperature Control Systems
- Temperature Control Islands: Combine water purifiers, chillers, and high-pressure cooling units for closed-loop control. Examples:
- High-Pressure Mold Coolers: Cool large areas (e.g., cores/slides).
- Precision Spot Coolers: Target hotspots (e.g., inserts) with intermittent high-pressure water to eliminate shrinkage.
- RO Water Systems: Prevent clogging via reverse osmosis.
- Smart Features: Zone-specific control (independent timing/flow/delay settings) and synchronization with die-casting machine signals.
5. Modular Control Devices

- Mold Temperature Controllers (MTCs):
- Water-Based MTCs: For temperatures <160°C (e.g., aluminum alloys).
- Oil-Based MTCs: For >160°C (e.g., magnesium/copper alloys).
- Spot Coolers: Localized cooling with high-pressure water or RO-treated water to avoid clogs.
6. Intelligent Control Modes
- Medium Temperature Control: Directly adjust water/oil temperature (common for most applications).
- Mold Surface Temperature Control: Use embedded thermocouples or thermal cameras for real-time PID-based precision regulation.
- Cascade Control: Combine medium and mold temperature signals for ultra-high precision in complex molds.
7. Auxiliary Heating Systems
- Electric Heaters/Radiant Heaters: Preheat molds but risk uneven heating.
- Thermal Oil Circulation: Heat molds to operating temperatures via MTCs to prevent molten metal solidification.
Also, you know what?
Mold temperature controller selection depends on alloy type (Al, Mg, Cu), mold complexity, and production cycles. Modern trends favor integrated systems (e.g., temperature control islands) and smart automation (PID + sensor-based closed-loop) to optimize thermal balance and extend mold life. For example, unified systems integrate hardware (valve manifolds, pump stations) and software (data logging, alarm tracking), reducing footprint and enhancing process stability.
How to determine mold temperature?
We have combined Haichen’s decades of design practice with mold temperature control and gained a lot of valuable experience.
Are you unfamiliar with the concept of die casting mold temperature?Just like quality control in many molding manufacturing industries, temperature control is an extremely important part.
To determine mold temperature, consider material properties, product design, measurement methods, and equipment selection. Here’s a structured approach:

1. Refer to Material-Specific Guidelines
Different metal materials require different temperature settings and management
- Plastic materials have specific mold temperature requirements. Examples:
- LCP:
- Thin-walled parts: 60–100°C (cycle time priority), 100–150°C (flow/weld strength), or >160°C (surface finish).
- Radel/Acudel (engineering plastics): 120–160°C (higher for glass-filled grades).
- POM:
- General: 80–120°C; precision parts: 120°C; impact-resistant grades: <80°C.
- Polyurethane: ≥80°F (27°C), ideally 100°F (38°C).
2. Analyze Product and Process Requirements
Extensive manual quality control is often more effective.
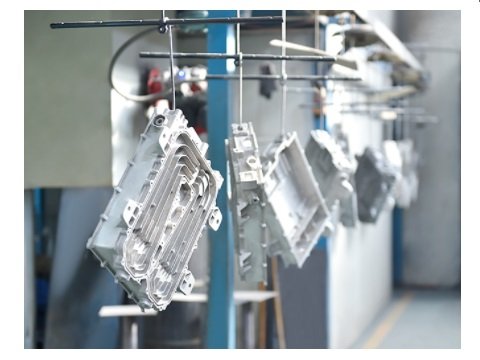
- Complex geometries/thin walls: Higher temperatures improve flow (e.g., LCP).
- Surface quality:
- High-gloss finishes or textures require higher front mold temperatures (e.g., front mold 20–30°C hotter than rear, up to 40–180°C).
- Ejection challenges: Lower temperatures reduce sticking for intricate parts.
3. Implement Multi-Point Temperature Measurement
The more temperature control points the better, you have to combine them with the actual effects.
- Measurement locations: Follow ASTM standards (center, near edges, intermediate points).
- Tools:
- Contact sensors: Embedded thermocouples (note: cavity vs. mold temperature differences).
- Non-contact: Infrared thermal imaging (suitable for reflective surfaces) or measure part temperature post-ejection.
- Data logging: Use portable IR thermometers (e.g., PGM+) for historical analysis.
4. Select and Calculate Temperature Control Equipment
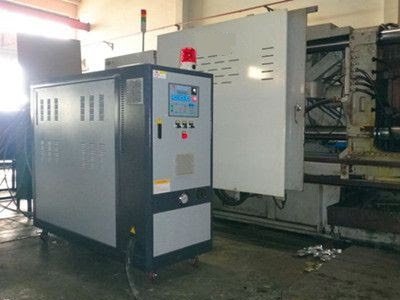
- Heating/cooling power:
- Heating:
Power (kW)=Mold weight (kg)×Specific heat×ΔT(°C)×Safety factor (1.5–2)Heating time (s) \times1000Power (kW)=Heating time (s) \times1000Mold weight (kg)×Specific heat×ΔT(°C)×Safety factor (1.5–2). - Cooling: Based on part weight, cycle time, and material-specific heat.
- Heat transfer medium:
- Water-based systems for ≤120°C; oil-based for >200°C.
- Cooling channel design: Optimize length, diameter, and layout for thermal uniformity.
5. Optimize and Validate
- Trial-and-error: Adjust temperatures and inspect part quality (e.g., warpage, sink marks).
- Simulation: Use mold cooling analysis software (e.g., Moldflow) to predict thermal distribution.
- Process monitoring: Track coolant inlet/outlet temperatures for stability.
6. Address Special Cases
- High-temperature materials:
- E.g., PPSU requires mold temperatures 20–50°C above melt point (range: 23–180°C).
- Glass molds: Use infrared sensors for transient thermal monitoring; control air cooling and lubricants.
Better note these
- Uniformity: Prevent hot/cold spots using insulation plates and balanced coolant flow.
- Dynamic adjustments: Real-time monitoring (e.g., predictive models vs. sensor data) to detect anomalies.
By integrating material data, process needs, and advanced measurement tools, mold temperature can be precisely controlled for optimal product quality and efficiency.
Temperature control of Haichen die casting machine
Next, we will focus on our rich experience in temperature control.
After more than 20 years of development and design, Haichen die casting machines integrate digital control, automation and precision engineering to achieve stable temperature management, ensuring efficient operation and consistent product quality.
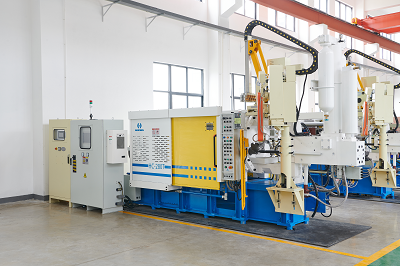
1. Different die casting Alloy Melt Temperature Control
- Digital Furnace Control: Equipped with digitally regulated furnaces, Haichen machines precisely adjust melting temperatures. For example, aluminum alloys are typically melted at 650–710°C, with parameters dynamically optimized for part geometry (e.g., thin/thick walls) to balance fluidity and solidification shrinkage.
- High-Temperature Components: Nozzles and gooseneck components use corrosion-resistant, high-temperature steel to maintain stability during high-pressure injection.
2. Mold Temperature Management
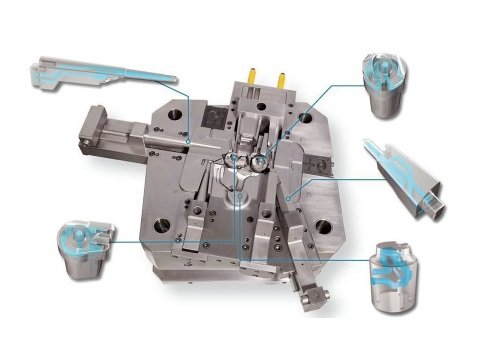
- Preheating & Operating Temperatures: Molds are preheated to 150–200°C (for aluminum alloys) to prevent rapid cooling of molten metal and reduce thermal stress. Operating temperatures are maintained between 180–280°C, adjusted based on alloy type and casting requirements.
- Smart Temperature Control: PLC units and LCD touchscreens enable real-time monitoring and parameter adjustments. Systems often feature PID auto-tuning, dynamically regulating cooling/heating media flow (e.g., water/oil) to minimize deviations between measured (PV) and target (SV) temperatures.
- Cooling Technology: Multi-channel cooling systems combine water cooling (for low-temperature zones) and oil cooling (tolerant up to 360°C). Intermittent cooling and compressed air purging prevent residual moisture and defects. Complex molds may use temperature control island technology for zone-specific cooling.
3. Hydraulic System & Auxiliary Controls
- Hydraulic Oil Temperature: Maintained at 30–55°C via proportional valves to stabilize pressure/flow and optimize energy efficiency.
- Automated Spraying & Cycle Control: Consistent cycle times (e.g., pouring to part ejection) minimize temperature fluctuations. Release agent spray volume is auto-adjusted based on mold temperature to avoid overuse or undercoating.
4. Advantages & Quality Assurance
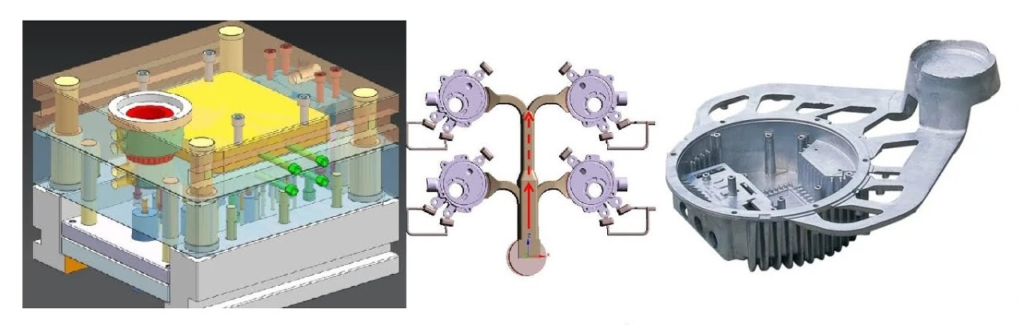
- Extended Mold Life: Precise thermal management reduces stress and surface cracks, increasing mold lifespan by 30%+.
- Defect Reduction: Balanced heat distribution (e.g., sequential solidification) minimizes shrinkage pores, gas traps, and improves dimensional accuracy/surface finish.
- Energy Efficiency: Dual-pump or single-pump energy-saving designs, combined with smart cooling, reduce water and release agent consumption.
5. Standards & Innovations
- Complies with national standards (e.g., nozzle temperatures: 380°C for zinc alloys, 650°C for magnesium alloys). Innovations like temperature control islands and integrated mold temperature machines drive the industry toward intelligent, high-precision production.
Haichen’s temperature control system leverages digitalization, automation, and advanced cooling strategies to holistically manage melt, mold, and hydraulic temperatures, ensuring both productivity and part quality in die casting processes.
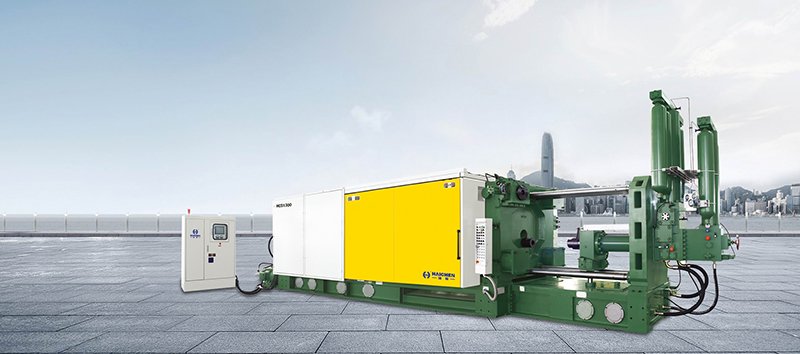
Contact us for more technical details about die casting.