The role of the chillers used in casting
In the casting process, the chillers are mainly used to control the cooling rate and directional solidification of the casting to improve the quality and mechanical properties of the casting.
Chillers accelerate solidification in specific areas by rapidly absorbing heat, thereby reducing defects in castings such as craters, porosity, and cracks.
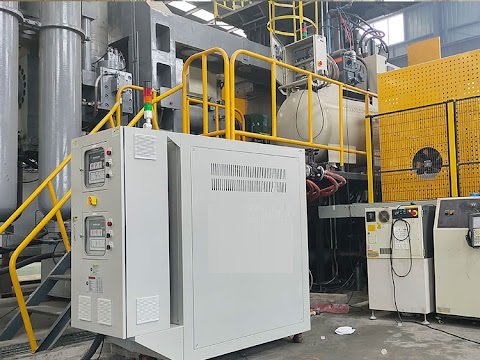
Controlling the mold temperature
The chillers ensures thermal balance by adjusting the temperature of the mold, thereby improving the quality and production efficiency of die castings.
Improve product quality
A reasonable cooling system can effectively control the solidification process of castings and reduce the occurrence of defects.
Such as porosity and inclusions, and surface defects such as thermal cracks and porosity.
so as to improve the quality and reliability of products.
For example, in aluminum alloy die casting, the use of water cooling technology can significantly improve the compactness of the die casting, reduce the air leakage rate, and reduce the scrap rate.
Improve production efficiency
The optimized cooling system can speed up the cooling rate of castings, shorten the production cycle, and improve production efficiency and productivity.
For example, a mold that is not water-cooled can only produce 50-60 castings per hour.
While a mold that is water-cooled can produce 100-120 pieces per hour, which is a doubling increase in productivity.
Extend the life of the mold
For example, the mold core jet cooler with fine hole cooling developed abroad can effectively improve the core life and die casting quality even at high temperatures.
Defect reduction
The design and optimization of the cooling system plays an important role in reducing the distribution of shrinkage cavities in castings, reducing porosity, and improving the quality of castings.
For example, in complex die casting molds, adjusting the amount of cooling water and temperature can change the distribution of shrinkage porosity in the casting, thereby reducing the porosity of the casting.
Improve the mold temperature field
improve the cooling efficiency by reasonably arranging the cooling water channel so that the cooling water channel is as close to the cavity surface of the mold as possible.
The arrangement of the cooling channel should be uniform and symmetrical to avoid local overheating or overcooling.
Protecting equipment
Cooling systems are essential to protect critical equipment and ensure the production of high-quality components.
Different metals have different optimal forging temperature ranges, beyond which defects can lead to defects in the final product.
Protect critical equipment and ensure the production of high-quality components.
Control Solidification Sequence
Coolers, gate systems and risers can control the solidification sequence of the castings and increase the effective feed distance of the risers.
This helps to change the solidification order of the casting so that it solidifies in order
Thus reducing the formation of craters and porosity.
Increase the temperature gradient
The cooler is placed in the mold to increase the temperature gradient during the solidification process, making the solidification sequence of the casting more obvious.
This temperature gradient facilitates directional solidification, allowing the casting to shrink more evenly during cooling.
Accelerated local solidification
The cooler accelerates the solidification of the local thick-walled part of the casting by absorbing heat.
So that it solidifies at the same time as the surrounding part.
thereby eliminating local thermal stress and preventing the formation of cracks.
This accelerated solidification effect is especially useful in areas where it is difficult to install risers, and can effectively prevent craters and porosity.
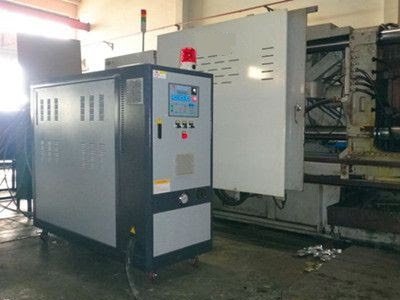
Improves casting hardness and strength
Coolers can also increase the hardness and strength of localized areas of the casting by setting quickly.
This is because the rapid solidification freezes the duplex film, keeping it compact, which improves the overall mechanical properties of the casting.
Chillers affect die casting
Cooling rate
Cooling rate is one of the key factors affecting the hardness and strength of castings.
Rapid cooling allows for grain refinement, increasing the continuity of grain boundaries and thus increasing the hardness of the material.
However, too fast cooling can also lead to increased internal stresses and even cracks. Therefore, controlling the proper cooling rate is essential to achieve the desired hardness and strength.
Selection of cooling medium
Different cooling media such as water, oil, brine, etc., have a significant impact on the cooling rate and final quality of molten aluminum castings due to their different thermal conductivity.
Choosing the right cooling medium can effectively prevent the concentration of thermal stress caused by uneven cooling and reduce the risk of cracking in castings.
Haichen Chiller applications
In actual production, the production efficiency and product quality of die castings can be significantly improved by applying a cooler.
For example, Haichen can offer dozens of different models of coolers for foundries to choose from.
The application of chiller not only improves the performance of die castings.
but also provides an important reference for research and practice in related fields.
