Die casting alloys refer to the metal material made by injecting molten metal into the mould through high pressure. They mainly include aluminium alloys, zinc alloys, lead alloys, magnesium alloys and copper alloys.
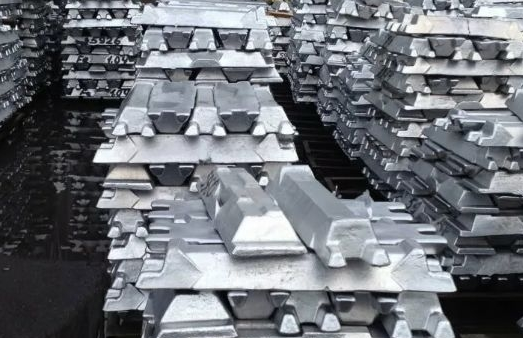
These alloys have good die-casting properties, corrosion resistance, high strength and low density, and are widely used in automotive, aerospace, electronic equipment and other fields.
According to a variety of die-casting alloy melting point of different physical characteristics in the actual industrial production will have different die-casting process for subdivision.
Routinely speaking, the melting point of zinc alloy, lead alloy is the use of hot chamber die casting machine to carry out the processing of production.
Cold chamber die casting process to deal with aluminium alloys, magnesium alloys such as higher melting point alloy materials.
Application areas of zinc alloy die casting
Zinc alloy die casting has a wide range of applications.
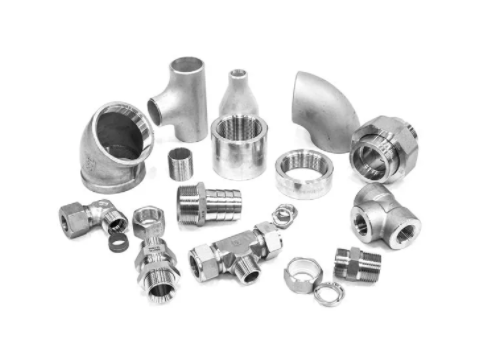
It mainly includes six aspects:
- Automotive industry
- Electronic communication industry
- Home and construction industry
- Toys and gifts industry
- Medical equipment industry
- Hardware tools industry
Automotive industry:
Manufacture engine parts, transmission parts, body structure parts, decorative parts, etc.
Electronic communication industry:
Manufacture zinc alloy shells, connectors, heat sinks, etc. for electronic equipment.
Home and construction industry:
Zinc alloy die-casting production of door and window hardware fittings, furniture fittings, bathroom hardware, architectural decorative parts, etc.
Toys and gifts industry:
Die-casting zinc alloy to make all kinds of toys and gifts crafts.
Medical equipment industry:
Die-casting zinc alloy to produce surgical instrument handles, medical stents and so on.
Hardware tools industry:
Zinc alloy die casting manufacturing tool handle and tool accessories.
Zinc alloy die casting has become an indispensable material choice for many industries due to its high strength, heat resistance, precise size and wear resistance.
Product advantages of die-cast aluminium alloys
Aluminium die casting materials are a large part of the entire die casting industry.
It is used in a wide range of fields, the product performance is good is many industrial fields essential workpiece materials.
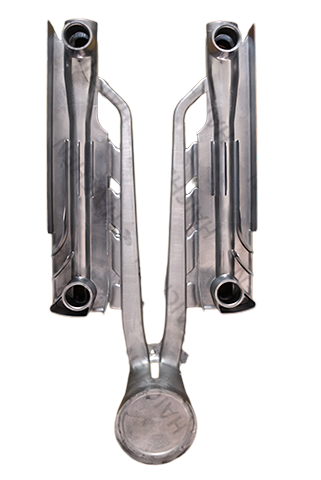
The product advantages of die-casting aluminium alloy include seven major aspects:
- Lightweight
- High strength and corrosion resistance
- High precision and complex shape manufacturing ability
- Excellent thermal and electrical conductivity
- High production efficiency
- Cost-effective
- Environmental protection and sustainability
Lightweight:
Aluminium alloy density is small, high strength, can significantly reduce the weight of the product, improve fuel efficiency and electric range.
High strength and corrosion resistance:
Aluminium alloy die casting has high mechanical strength and good corrosion resistance, applicable to a variety of harsh environments.
High precision and complex shape manufacturing ability:
Aluminium alloy die casting process can achieve high precision and complex shape of a molding, to meet the diversified design needs.
Excellent thermal and electrical conductivity:
Aluminium alloy has excellent thermal and electrical conductivity, suitable for heat sinks, electronic packaging and other fields.
High production efficiency:
Aluminium alloy die-casting process with high degree of automation, production efficiency significantly improved, suitable for mass production.
Cost-effective:
Aluminium alloy material price is moderate, die-casting process can reduce material waste and labour costs, has high economic efficiency.
Environmental protection and sustainability:
Aluminium alloy can be completely recycled and reused, in line with the concept of circular economy.
These advantages make aluminium alloy die casting in automotive, aerospace, electronic equipment and many other fields are widely used.
How to choose die casting machine for different die casting alloys
Selection of die-casting machine, according to the type of die-casting alloy, casting size, weight, precision requirements and production batch and other factors to consider.
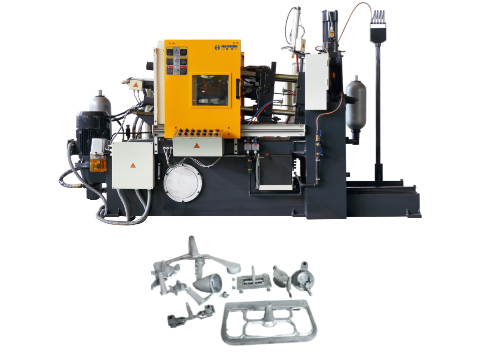
Different alloys applicable die-casting machine type is as follows:
- Zinc alloy, tin alloy, lead alloy and small magnesium alloy
- Aluminium alloy, copper alloy and large magnesium alloy
- Vertical cold chamber die-casting machine
- Horizontal cold chamber die-casting machine
- All-hydraulic die-casting machine
- High degree of automation die-casting machine
Zinc alloy, tin alloy, lead alloy and small magnesium alloy:
Usually choose hot chamber die casting machine.
Because it is suitable for low melting point alloy, and can shorten the cycle time, improve production efficiency.
Aluminium alloy, copper alloy and large magnesium alloy:
General use of cold chamber die-casting machine.
Because it is suitable for high melting point alloy, and can reduce the metal liquid heat loss and oxidation inclusions.
Vertical cold chamber die-casting machine:
Suitable for the shape of the centre of the radial or cylindrical castings, suitable for opening the centre of the gate.
Horizontal cold chamber die-casting machine:
High production efficiency, suitable for all kinds of non-ferrous alloys, especially suitable for castings with eccentric gate or centre gate.
All-hydraulic die-casting machine:
Suitable for many varieties, small batch production, but the tonnage is small, clamping reliability need to pay attention to.
High degree of automation die-casting machine:
For less varieties, large batch production.
Should choose mechanisation, high degree of automation model, in order to improve production efficiency and reduce costs.
Comprehensive consideration of alloy characteristics, process parameters, mould size and production requirements.
Scientific selection of suitable die-casting machine models and specifications, in order to ensure product quality and production efficiency.
Haichen die casting machines meet the production needs of different die casting alloys
Our die casting machines are capable of meeting the production requirements of different die casting alloys.
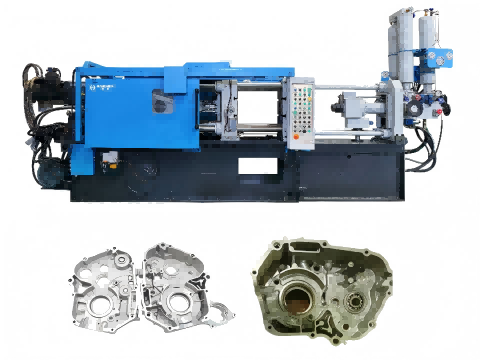
Different types of cold chamber and hot chamber die casting machines have been designed to handle a wide range of materials and to suit different applications.
Haichende die casting technology enables the efficient production of aluminium, zinc and magnesium components with good mechanical properties.
Over many years of design practice, we have the ability to configure a complete alloy die casting line from die casting product design to mould design.
For more than 20 years, we have been providing complete solutions to customers all over the world.
Welcome to write to us at any time, let us understand your needs and give you the perfect solution.