High-pressure and low-pressure die casting differences primarily in the applied pressure, range of application and casting characteristics.
Die casting is a versatile manufacturing process used to produce metal parts with high precision and consistency. Within the die casting industry, two primary methods stand out: high pressure die casting (HPDC) and low pressure die casting (LPDC). Each method has its own unique characteristics, advantages, and applications.
Low-pressure die casting is suitable for large thick-walled parts with high internal quality requirements. And High-pressure die casting is suitable for thin-walled parts with complex shapes.
In this article, we will explore the key differences between high pressure and low pressure die casting and how HAICHEN, as a leading die casting machine manufacturer, offers solutions tailored to both processes.
High-pressure die casting differences
- Application areas of high-pressure die casting
- Advantages of High-Pressure Die Casting

High pressure die casting is a process that uses extremely high pressure to inject molten metal into a mold. The high pressure ensures that the metal completely fills the mold cavity, resulting in a dense, fine-grained casting with good surface finish and dimensional accuracy.
Application areas of high-pressure die casting
High-pressure die casting is commonly used for aluminum and zinc alloy materials for applications in the automotive, electronics, and consumer goods industries.
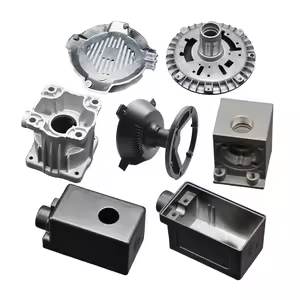
Advantages of High-Pressure Die Casting
- High production efficiency
- Good surface quality of castings
- High dimensional accuracy
- High material utilization
- uitable for complex and thin-walled parts
- High production efficiency:
High-pressure die casting machines can quickly fill molds, shorten production cycles, and are suitable for large-scale production. - Good surface quality of castings:
High pressure allows metal to flow more fully, reduces bubbles and defects, and improves the surface finish of castings. - High dimensional accuracy:
High pressure helps metal fill every corner of the mold, reduces shrinkage and deformation, and improves the dimensional stability of castings. - High material utilization:
Because the strong filling capacity of high-pressure die casting, material waste can be reduced and material utilization can be improved. - uitable for complex and thin-walled parts:
High-pressure die casting is suitable for the production of complex-shaped, thin-walled castings, such as automotive parts and electronic products.
Low-pressure die casting differences
- Application areas of low-pressure die casting
- Advantages of low-pressure die casting
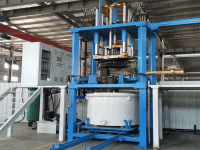
Low-pressure die casting operates at significantly lower pressures, typically between 0.1 and 0.5 MPa. Lower pressures result in fewer internal defects in castings, such as porosity and shrinkage, which can improve the quality of castings
Application areas of low-pressure die casting
Low-pressure die casting is often used for larger and thicker-walled parts, where slow filling of the mold allows for better control of the solidification process. It is also used for magnesium alloy materials, which are used in the aerospace and automotive industries for precision parts.
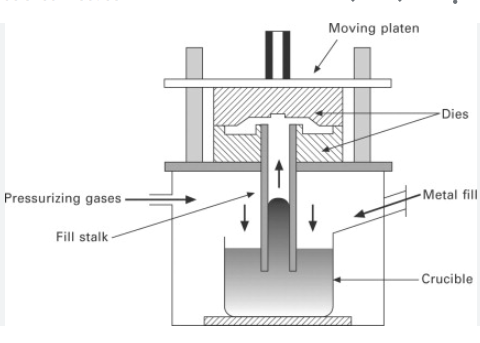
Advantages of low-pressure die casting
- High internal quality
- Suitable for large and thick-walled parts
- Reduced mechanical stress
- Suitable for high melting point materials
- High operating safety
- High internal quality:
The slow filling of low-pressure die casting helps reduce internal stress and defects.Improve the intrinsic quality of the casting. - Suitable for large and thick-walled parts:
Low-pressure die casting is suitable for the production of large and thick-walled castings. Because slow filling helps control thermal gradients and reduce thermal stress. - Reduced mechanical stress:
Due to the lower filling pressure, the mold and casting are subject to less mechanical stress.This helps to extend the life of the mold. - Suitable for high melting point materials:
Low-pressure die casting is suitable for materials with higher melting points. Such as magnesium alloys, because these materials may be difficult to fill under high pressure. - High operating safety:
Due to the low operating pressure, the operating safety of low-pressure die casting machines is relatively high, reducing operating risks.
High-pressure and low-pressure die casting differences
The following table shows the comparison between low pressure die casting and high pressure die casting:
Main differences | High-pressure die casting | Low pressure die casting |
Pressure | Tens to hundreds of MPa | 0.1 to 0.5 MPa |
Casting quality | Higher internal stresses and porosity | Produces castings with fewer internal defects |
Mold life | Faster wear | Longer life |
Material compatibility | Aluminum and zinc alloys | Aluminum, zinc, magnesium alloys |
Cost and efficiency | Faster cycle times | Higher cost and slower speed |
Application | Complex, thin-walled parts | Higher quality requirements, thicker parts |
Haichen Machinery: High Pressure Die Casting Machine Manufacturer
The die casting difference of Haichen high pressure die casting machine is reflected in the use of efficient design,
It ensures fast cycle time and high production efficiency, suitable for large-scale production needs.
Equipped with advanced control system, it can accurately control injection pressure and speed to ensure the consistency and quality of castings.
Using high-quality materials and precision manufacturing process, Haichen high pressure die casting machine has excellent durability and reliability, reducing maintenance costs and downtime.
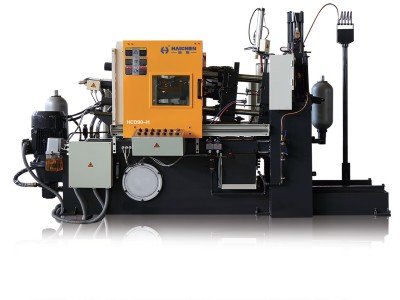
Although there are huge die casting differences between high pressure die casting and low pressure die casting, they each have their own unique advantages and applicable scenarios.
It is necessary to select the appropriate die casting technology, taking into account factors such as casting design, material properties, production efficiency and cost.