Cooling chiller function in casting is to remove excess heat generated during the casting process to ensure that the machinery, dies, and molten materials operate within their optimal temperature ranges.
In the casting process, the cooler (chiller) is a device to accelerate the solidification of castings. The main role of the cooler is to control the solidification rate of the casting through rapid cooling, thus improving the microstructure and mechanical properties of the casting.
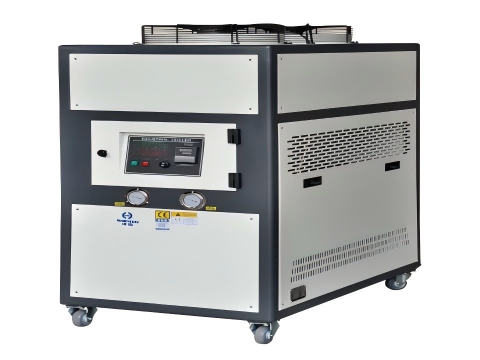
Cooling chiller function in casting
Accelerated solidification
- accelerating the solidification process of castings.
- By placing coolers in the mold, the local cooling rate can be increased. Thereby improving the cooling efficiency of the casting.
- For example, an external cooler accelerates solidification by absorbing the heat generated by the superheated fluid and the latent heat of the alloy. Prevents castings from developing shrinkage and porosity at hot spots.
Improvement of microstructure
- Coolers can influence the microstructure of castings.
- For example, the use of a cooler can improve the surface hardness and the uniformity of the microstructure.
- In addition, coolers can be used for surface hardening to give the casting surface higher hardness and wear resistance.
Controlling Thermal Stress
- By controlling the cooling rate, coolers help to reduce the thermal stresses within the casting, thereby reducing the risk of cracking.
- For example, in a continuous casting process, coolers are used to maintain a stable temperature inside the mold to reduce stress concentrations due to temperature variations and prevent cracking.
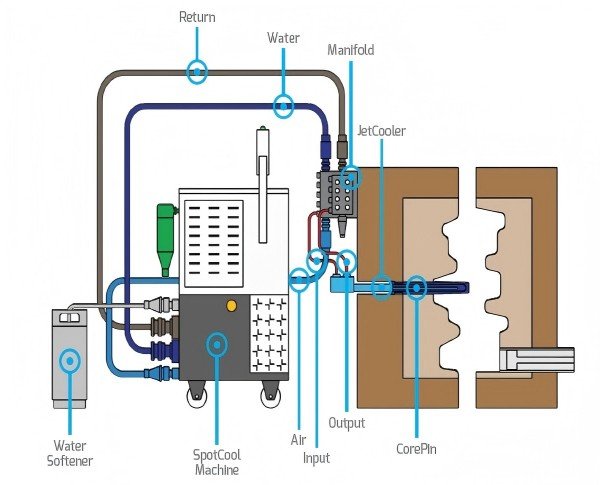
Increased productivity
- Coolers can significantly reduce the cooling time of castings, thereby increasing productivity.
- For example, in injection molding, coolers can reduce cooling times by 30-50%, thus speeding up the pace of production.
Optimizing casting quality
- By precisely controlling the cooling process, coolers help to improve the overall quality and consistency of castings.
- For example, in sand casting, the mechanical properties and surface quality of castings can be improved through the use of skeleton sand design and water spray cooling technology.
Environmental control and worker safety
- In the metal and steel manufacturing industries, the heat generated during production can create difficult working conditions.
- Industrial coolers also help control ambient temperatures and maintain safer, more comfortable working conditions.
Haichen die casting machine cooling chiller
Haichen Machinery, based in Ningbo, China, specializes in manufacturing cold chamber die casting machines and hot chamber die casting machines. We also offer auxiliary equipment including cooling chiller to enhance automation in the die casting process.
If you have any questions about die casting machine and die casting cooling chiller. Please feel free to consult us, we can provide more information and offer.
Cooling chiller plays a multifaceted role in the foundry process, from controlling the solidification structure of the metal to supporting the heat treatment process to environmental control.
By providing efficient and reliable cooling, these coolers help metal producers optimize their processes, improve energy efficiency, and ensure the long-term sustainability of their operations.