In the die casting process, the importance of cooling cannot be ignored. Because the design and efficiency of the cooling system directly affects the quality of die castings, production speed and mold life.
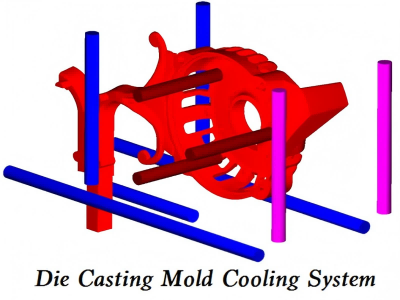
The importance of cooling in die casting
Cooling is a critical component of the die casting process. It ensures proper solidification, reduces cycle time, extends die life, enhances product quality, and helps to maintain a stable and efficient production environment.
Ensuring Proper Solidification
Cooling helps the molten metal solidify quickly and uniformly. This is crucial to prevent defects such as shrinkage porosity and warping.
When the metal cools too slowly, it may not fill the mold cavity completely, leading to incomplete or defective parts. By controlling the cooling rate, manufacturers can ensure that the casting achieves the desired shape and dimensions.
Reducing Cycle Time
Effective cooling significantly reduces the cycle time in die casting. Faster cooling means that the casting can be ejected from the mold more quickly, allowing for more parts to be produced in a given time period.
This increased production rate enhances overall manufacturing efficiency and productivity.
Extending Die Life
The die, or mold, used in die casting is subjected to high temperatures during the process. Proper cooling helps to manage these temperatures and reduce thermal stress on the die. By minimizing thermal stress, the die can last longer, reducing maintenance costs and downtime.
This is particularly important in high-volume production runs where consistent quality and reliability are essential.
Enhancing Product Quality
Uniform cooling leads to better product quality. It helps to minimize defects such as porosity, cracks, and distortions, resulting in stronger and more durable castings. Additionally, precise cooling can improve the surface finish of the casting, meeting higher industry standards.
Controlling Thermal Environment
Cooling systems help to maintain a consistent thermal environment within the die casting machine. This is important for the overall stability and accuracy of the process. By keeping the mold and the surrounding equipment at a controlled temperature, manufacturers can avoid issues such as overheating and equipment failure.
Reducing Environmental Impact
Advanced cooling systems can also contribute to sustainability goals. Efficient cooling reduces energy consumption and waste by minimizing defects and optimizing cycle times. This not only lowers operational costs but also helps to reduce the environmental footprint of the manufacturing process.
Haichen die casting cooling system
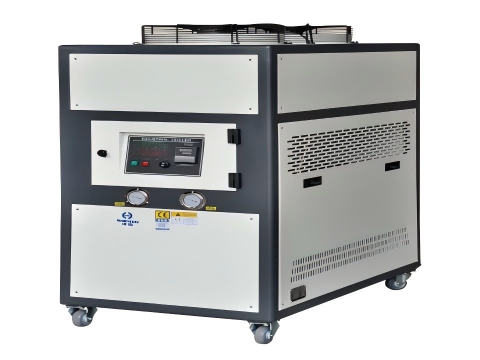
Haichen die casting cooling system is designed to optimize the casting process by ensuring efficient heat management, precise temperature control, and high-quality production. Here are the key features and benefits of Haichen’s cooling system:
Intelligent Temperature Control and Monitoring
Haichen’s cold chamber and hot chamber die casting machines are equipped with thermocouples to monitor mold temperature in real time. The built-in intelligent system compares the actual temperature with the set value and automatically adjusts the cooling water solenoid valves.
Efficient Cooling Channel Design
Haichen uses a multi-channel cooling system with Φ10 mm cooling water channels distributed along the cavity length. These channels are strategically placed to ensure uniform cooling, especially in thick-walled castings.
Structural Optimization and Dynamic Analysis
Finite element analysis is conducted during the design stage to enhance the cooling effect and reduce thermal deformation.