Application of cooling chiller in die casting can control mold temperature, improve product quality, extend mold life and optimize production efficiency.
A chiller is a mechanical device, it uses for refrigeration. Its main function is to remove heat from a system through a refrigeration cycle and discharge it to the external environment. Chillers widely use in commercial buildings. Also in industrial facilities, data centers and other places. That to provide cooling water for air conditioning systems to regulate indoor temperature and humidity.
In the die casting process, the design and application of the cooling system is of great significance to improving product quality, extending the life of the mold and improving production efficiency. The cooling system usually controls the mold temperature through water cooling or other cooling media to achieve fast and uniform cooling effect.
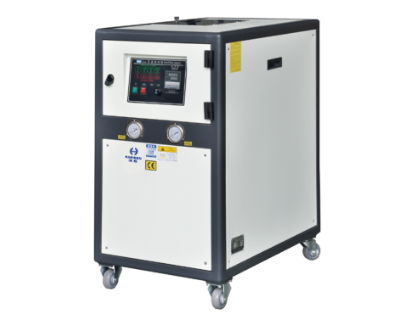
The role of the cooling chiller in die casting application
The cooling system reduces casting defects (such as pores, shrinkage and deformation) by lowering the mold temperature to achieve rapid solidification of the molten metal, thereby improving the mechanical properties and surface quality of the casting. In addition, the cooling system can extend the life of the mold and reduce thermal fatigue and wear caused by high temperature.
Classification of cooling chiller die casting methods
Common cooling methods include water cooling, oil cooling and air cooling:
- Water cooling: Heat is removed by circulating water flow. It is suitable for occasions requiring uniform cooling. This method is efficient. But it requires regular maintenance to prevent leakage or blockage.
Oil cooling: High-temperature oil (200-300°C) uses to cool the mold. It is suitable for occasions requiring high thermal stability, such as magnesium alloy die casting. However, oil cooling may cause fire risks and is more complicated to maintain.
Air cooling: Relying on air or ambient air for cooling. It is low-cost but less efficient. And it usually uses for small or low-volume production.
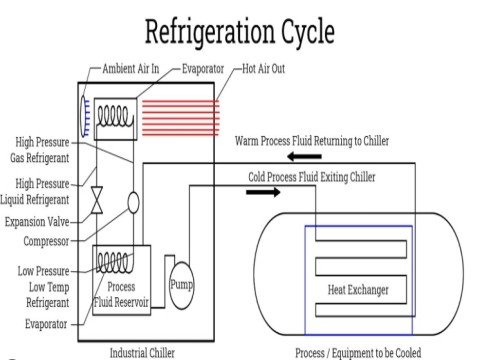
Advantages of Cooling chiller in die casting application
- Improve production efficiency
- Extend mold life
- Improve product quality
- Optimize surface quality
- Improve production efficiency: Rapid cooling can shorten the cycle time of the mold, thereby increasing production speed.
Extend mold life: By reducing the thermal stress caused by high temperature in the mold, the mold wear is reduced and the service life is extended.
Improve product quality: Uniform cooling helps to reduce casting defects such as pores, cracks and deformation, and improve the overall strength and durability of the casting.
Optimize surface quality: Precise temperature control can improve the surface finish of the casting and meet higher industry standards.
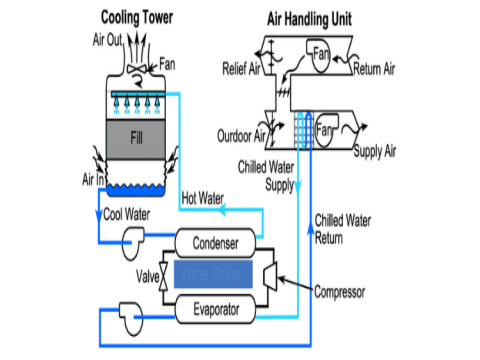
Design and optimization of cooling system
The design of cooling system needs to consider the geometry, material properties and production requirements of the mold. For example, the use of conformal cooling technology can significantly improve cooling efficiency and shorten curing time.
In addition, by optimizing the layout of cooling channels through CAE analysis, the uniform distribution of mold temperature can be achieved, thereby improving product quality.
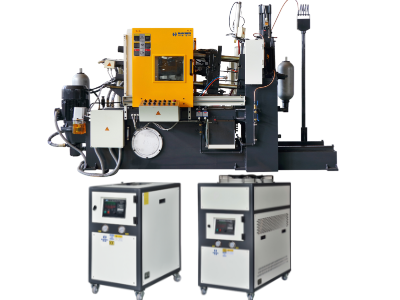
Maintenance and management of cooling system
The normal operation of the cooling system requires regular maintenance, including checking the sealing of the cooling pipes, cleaning the coolant and calibrating the temperature control system. In addition, the use of intelligent monitoring technology can monitor the mold temperature in real time to ensure the stability and reliability of the production process.
Innovation and development of cooling technology
In recent years, additive manufacturing technologies (such as SLM) have been used to design complex cooling channels. Furtherly, it can improve cooling efficiency and mold life.
In addition, the application of composite cooling irons has also shown potential in reducing defects and improving production efficiency.
The impact of cooling systems on production efficiency
An effective cooling system can shorten the production cycle, improve mold utilization, and reduce scrap rates. For example, in aluminum die casting, by optimizing the cooling design, it can significantly increase the production speed. It can also reduce energy consumption.
The application of cooling system in die casting process not only directly affects product quality and production efficiency, but also has a profound impact on mold life and equipment maintenance. Therefore, when designing and implementing cooling scheme, it is necessary to comprehensively consider the selection of cooling method, optimization of system design and details of maintenance management to achieve efficient and stable production goals.
Haichen die casting machine
Haichen is one Chinese die casting machine manufacturer for more than 10years. We produce both high pressure cold chamber die casting machine , hot chamber die casting machine and spare parts. They have durable and highly precise features.
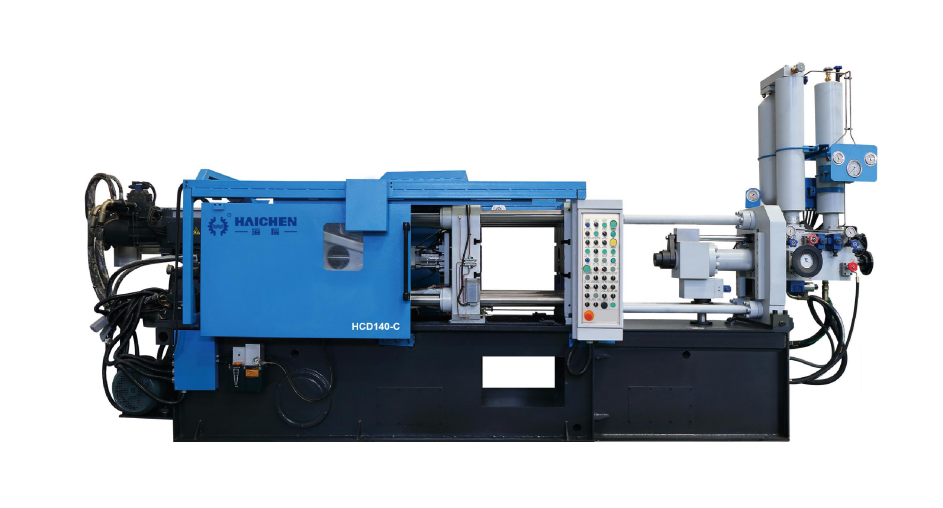
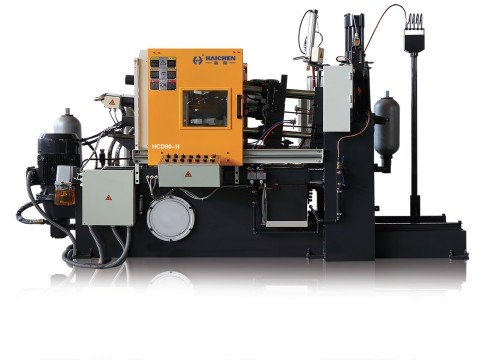
Haichen also produce die casting machine auxiliary equipment. Such as conveyor, vacuum machine, mold temperature controller, industrial robot, sprayer and so on.
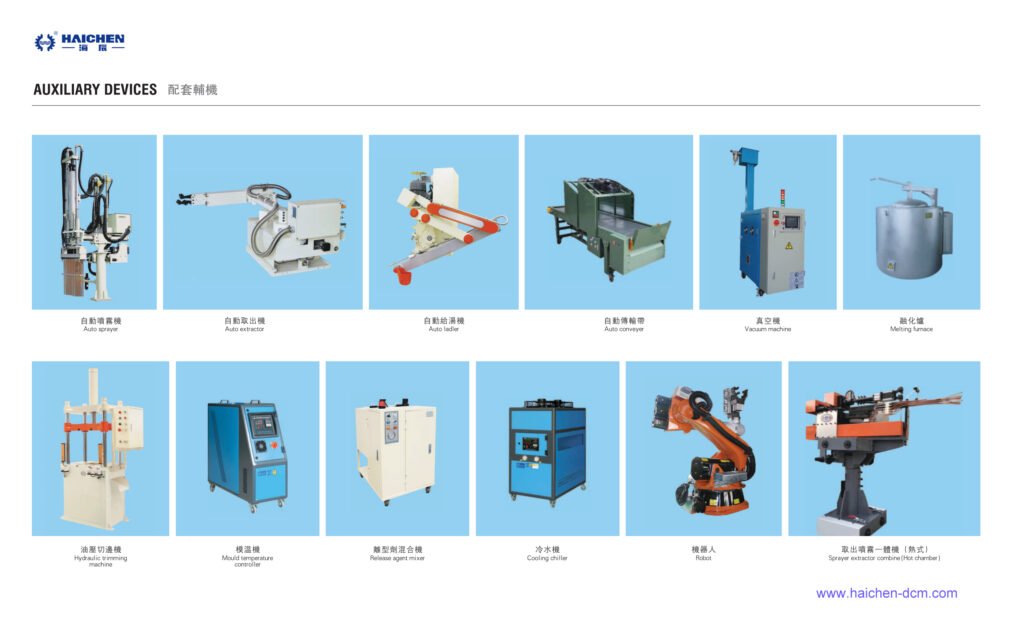
We supply cold chamber and hot chamber die casting machine spare parts.
Welcome contact us.