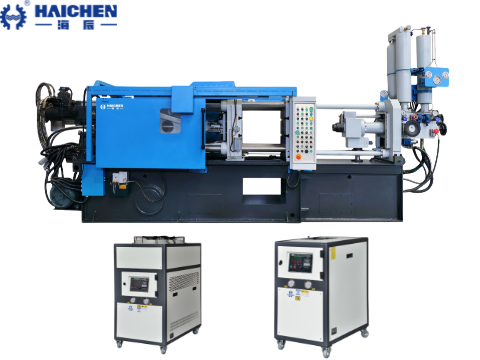
Interested in understanding the cooling chiller in die casting equipment components of the die casting industry?
The price range of chillers for die casting ranges from several thousand to tens of thousands of dollars.
After decades of involvement in the metal die casting industry, we have enough experience to tell that chillers are crucial to any industrial production line, especially metal processing equipment such as die casting.
As a well-known brand in the field of die-casting equipment, Haichen’s cooling system design focuses on high-precision temperature control, efficient heat dissipation and automated management.
The price system of chillers for die casting combines multiple factors in practical applications.
Price Influencing Factors
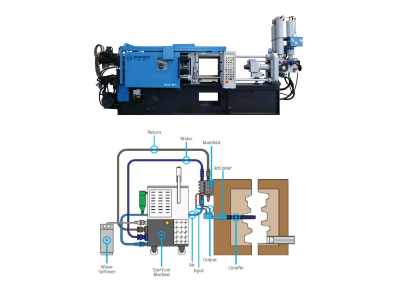
- Basic Models and Functions
- Conventional chillers cost 5,000 to 20,000 yuan, suitable for small/medium tonnage die casting machines (e.g., below 50T).
- High-end models (e.g., high-power cooling, corrosion-resistant materials, explosion-proof designs) range from tens of thousands to hundreds of thousands of yuan, serving special processes like magnesium/aluminum alloy production.
- Die Casting Machine Tonnage Correlation
- Chiller prices correlate directly with die casting machine tonnage or cooling capacity. For example, adding 10 tons to the die casting machine may raise chiller costs by 10,000–15,000 yuan (based on die casting machine tonnage pricing logic).
- Material and Customization Requirements
- Non-standard customization (e.g., stainless steel/titanium alloy materials, explosion-proof/waterproof designs) increase costs by 30%–50%.
Quality and Cost Trade-Off Recommendations
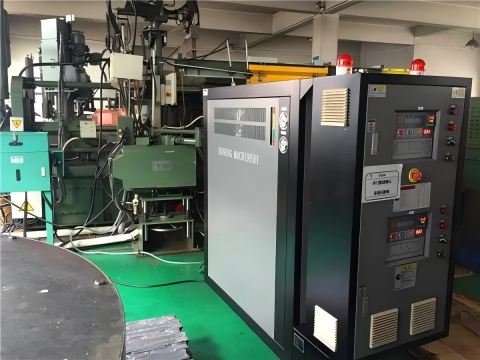
- Avoid Low-Price Traps
- Units priced below 5,000 yuan may include refurbished/second-hand equipment, low energy efficiency, or poor after-sales support. Avoid “scrapped machine modifications.”
- Core Considerations
- Prioritize refrigeration stability to ensure die-casting part yields. Opt for variable-frequency control or dual-circulation systems.
- Choose brands offering 24/7 technical support and lifetime maintenance to minimize downtime.
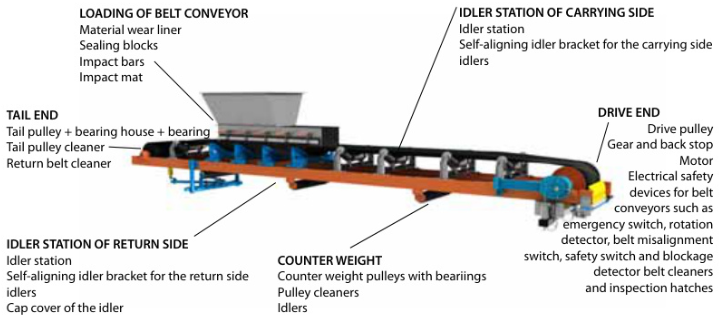
Purchasing Recommendations
- Conventional Needs
- For small/medium die-casting lines, select standard models (10,000–50,000 yuan) with an energy efficiency ratio (COP ≥ 3.0) and 304 stainless steel materials.
- High-End Needs
- For special alloys or continuous production, customize models (100,000–300,000 yuan) with 200kW+ cooling capacity and smart temperature control.
- Inquiry Process
- Provide die casting machine parameters (tonnage, cooling water temperature) to brands for accurate quotes. Request warranties exceeding 3 years.
Optional: To refine recommendations, share specific process parameters (e.g., die-casting materials, water circulation needs).
How does a cooling chiller work in die casting?
Integrated Cooling System Solutions for Die Casting (HAICHEN Custom Recommendations)
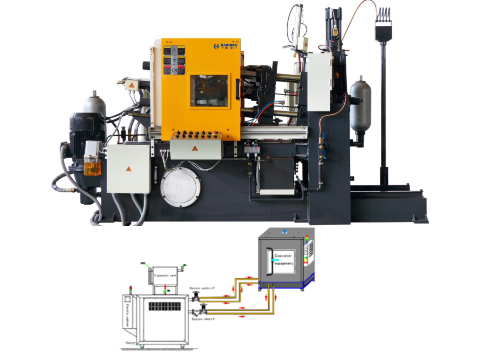
1. Precision Thermal Load Matching
HAICHEN engineers recommend three-stage thermodynamic simulation based on client-specific production parameters:
- Casting Parameters: Projected area (cm²) × Wall thickness (mm) × Alloy-specific heat capacity (kJ/kg·K)
- Process Parameters: Ejection temperature (°C) – Mold temperature setpoint (°C) = Effective cooling range
- Cycle Requirements: Single-part cooling time ≤ 80% of total cycle time
Case Study: For a new energy vehicle motor housing (ADC12 aluminum alloy), HAICHEN’s HCP-3000 dual-circuit chiller achieved 22% higher cooling capacity and 18% lower energy consumption compared to traditional systems.
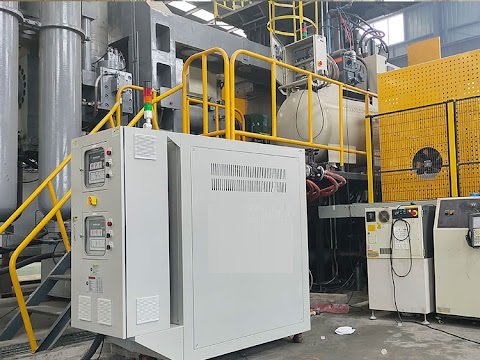
2. Proprietary Technologies
Technology Module | Key Advantages | Applications |
---|---|---|
Multi-stage Pressure Coupling | 5–25°C wide-range control, ±3% pressure stability | Thin-wall Mg alloy parts (<1.2mm) |
Dynamic Anti-fouling Algorithm | Reduces heat exchanger fouling to 0.0002 m²·K/W | Hard water regions (>300ppm TDS) |
Magnetic Levitation Inverter Compressor | 31% energy savings, noise ≤68dB | Medical precision die casting |
3. We have Full Lifecycle Service
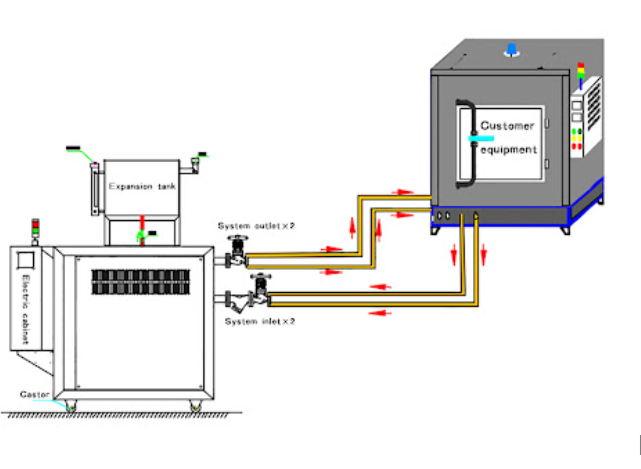
- Pre-installation Analysis
- Free mold thermal channel infrared imaging (0.1°C resolution)
- CAE-optimized cooling channel design (40% shorter development time)
- Installation & Commissioning
- ISO-certified cleanroom installation (160 m³/h air purity)
- 72-hour stress testing (including 10% overload conditions)
- Ongoing Support
- Remote monitoring of 16 critical parameters (e.g., evaporator approach temperature)
- Regional spare parts hubs (4-hour emergency response in Yangtze/Pearl River Delta)
4. Let ‘s Retrofit Project Benefits as a list.
Pre-retrofit Issue | HAICHEN Solution | Annual Savings |
---|---|---|
8% porosity in Zin alloy parts | HCD-200-H micro-pulse temperature control | Yield increased to 99.2%, saving ¥360,000 |
±7°C hydraulic oil fluctuations | HCR-50 waste heat recovery system | Oil stability ±1.5°C, 64% fewer failures |
150k-shot mold lifespan | HCS-1000 gradient cooling technology | Mold life extended to 280k shots, saving ¥2.1M |
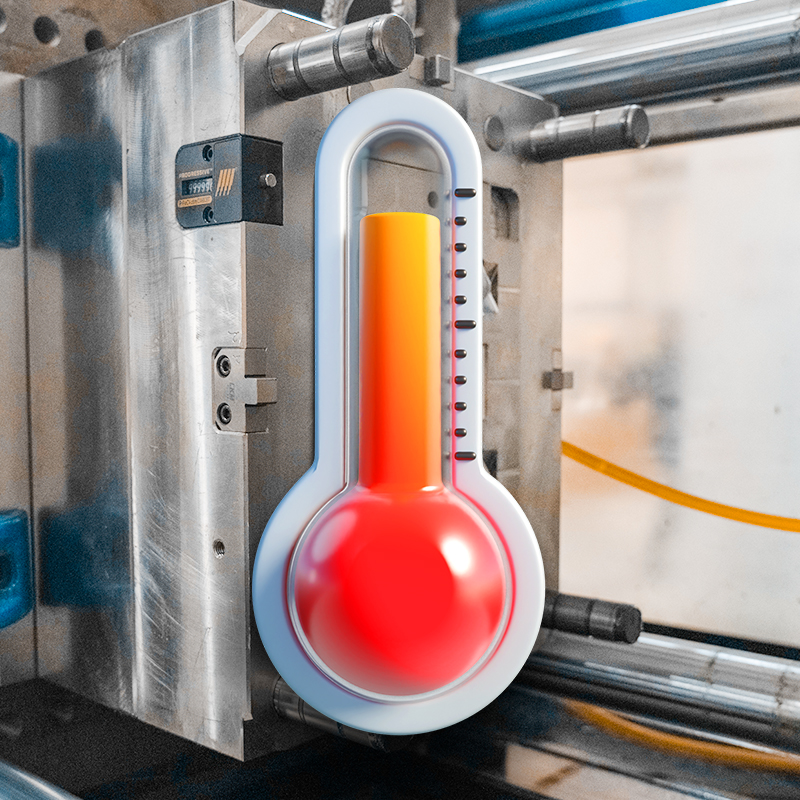
5. Sustainability Initiatives
- Carbon Footprint Management
- GB 19577-2019 Tier 1 energy efficiency certification
- 35% refrigerant reduction (microchannel condenser tech)
- Circular Economy
- Trade-in program: Up to 15% credit for old equipment
- Closed-loop water treatment: Zero wastewater discharge
HAICHEN Service Commitments
- 5-year warranty on core components (compressor, plate heat exchanger, PLC)
- Free quarterly preventive maintenance (condenser cleaning, electrical safety checks)
- Energy-saving guarantee: Performance shortfall compensation for high-volume clients (>1M parts/year)
For customized reports or on-site thermal balance testing, submit the Die Casting Process Parameter Survey (Doc: HC-TD-2023V2) to receive a preliminary proposal within 24 hours.
This framework integrates HAICHEN’s engineering expertise with actionable data, ensuring optimal cooling performance aligned with your operational and sustainability goals.
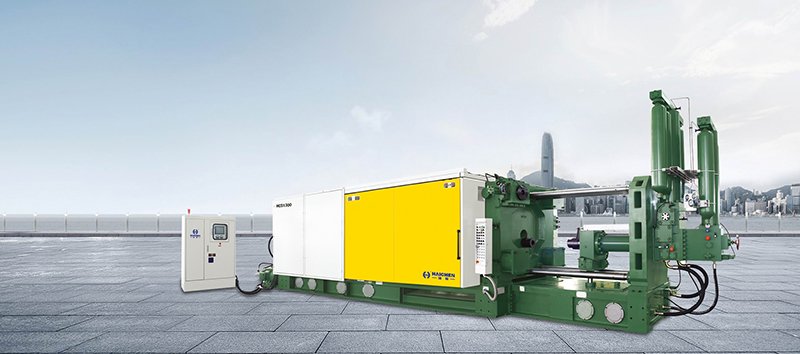
Contact Haichen anytime, we will ready for you.