Heat transfer
Heat transfer in die casting refers to the heat exchange process between the liquid metal and the mold during the die casting process.
This process has a significant impact on the quality and performance of the casting.
In the die casting process, liquid metal fills the mold cavity at high speed and solidifies under high pressure to form a casting.
The interfacial heat transfer behavior has a significant effect on the microstructure and mechanical properties of castings.
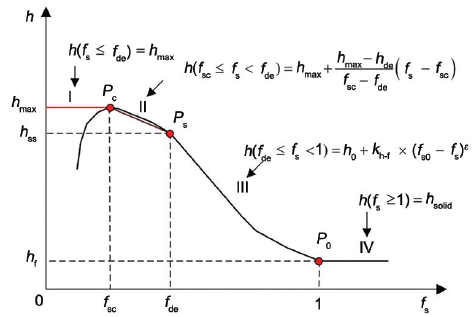
Heat Transfer Measurement Method
A specific measurement of the interfacial heat transfer coefficient (IHTC) in the die casting process through various experimental and computational methods.
Finite Element Analysis and Optimization Methods
Finite element analysis (FEM) combined with optimization method (FEM-OPT) was used to calculate IHTC.
In this method, the quantitative relationship between the heat transfer coefficient of the water-cooled interface of aluminum alloy.
And the change of temperature is realized through numerical simulation iterative calculation and automatic optimization.
Experimental design and numerical simulation
By designing the mold and casting process, accurately installing the pressure sensor and temperature measurement unit.
And carrying out extrusion casting experiments.
Establish a set of accurate measurement methods for mold temperature and interfacial pressure.
Discuss the performance of IHTC under different material and process conditions using a circular test model and Beck’s nonlinear estimation method.
Vacuum-Assisted High Pressure Die Casting (HPDC)
In the HPDC process, 18 thermocouples record time-varying temperature data on molds and castings.
And the IHTC and heat flux were calculated by program using the finite difference method.
Iterative formulas
Based on the least squares method and the thermal conductivity model, the iterative formula of IHTC is given.
A computer program completes the calculation of IHTC.
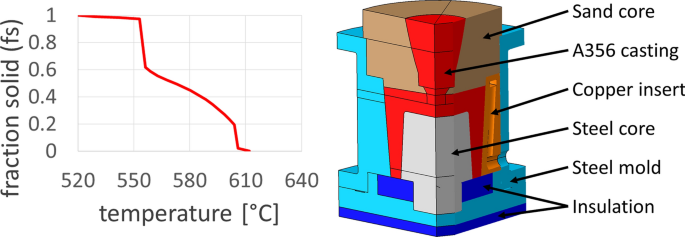
Improve heat transfer efficiency
Reducing the air gap between free interfaces to improve heat transfer efficiency is a complex and multifaceted task in die casting mold design.
Vacuum-assisted technology
Vacuum-assisted technology can significantly increase the interfacial heat transfer coefficient (IHTC) of castings.
Reduce the porosity of castings, and thus improve heat transfer efficiency.
Studies have shown that vacuum assistance can effectively reduce the porosity and particle size in castings.
Thereby improving the mechanical properties of castings.
Optimize mold temperature control
Mold temperature has an important influence on the heat transfer behavior in the die casting process.
By using high-performance multi-zone temperature control equipment.
Precise control of the mold temperature can be achieved to optimize the heat transfer process.
Preventing the alloy liquid from passing through the gap and affecting the normal production.
Efficient in-mold cooling system
The non-destructive heat dissipation process of the mold is achieved through the efficient in-mold cooling cycle.
Which can replace the traditional external cooling method.
This design method not only reduces thermal stress and impact on the die steel.
But also ensures an optimal temperature distribution.
For example, the integration of several independent circulation channels in the mold ensures the desired heat dissipation and even temperature distribution.
Exhaust valve design
Reasonable design of the position and width of the exhaust valve in the mold can effectively discharge the gas from the mold and reduce the formation of pores. This can be achieved through an automated design system, which avoids iterative calculations and improves design efficiency.
Increases the heat dissipation surface
Increasing the heat dissipation surface in a specific part of the mold, such as processing the heat dissipation mesh on the forming surface of the side slide, can improve the heat dissipation efficiency.
This method not only increases the heat dissipation area.
But also improves the heat transfer efficiency by optimizing the heat dissipation path.
Optimize the sprue system
By optimizing the design of the sprue system, a fast and uniform mold filling process can be achieved.
Resulting in fewer internal defects due to air entrapment or shrinking pores.
For example, the use of a runner system that is lightweight and has an increased surface area for a specific surface area can effectively control the local temperature.
Use additives and lubricants
Using additives that help release dissolved gases during the melting process and lubricate the mold after each casting can reduce porosity tendency.
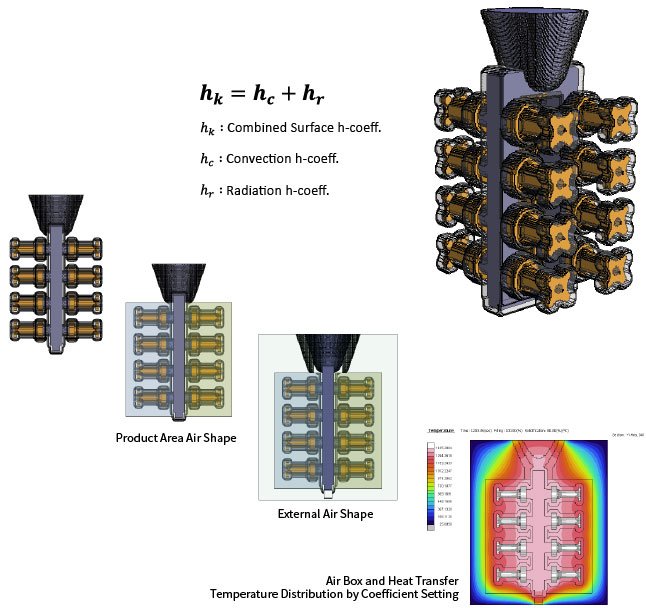
Haichen experience
The influence of different alloy types on the interfacial heat transfer coefficient in the die casting process is multifaceted.
Involving the chemical composition, process parameters, thickness and solidification rate of the alloy material.
The thermophysical parameters of the casting material, the experimental method and numerical simulation technology.